Table of Contents
- Introduction
- Editor’s Choice
- Global Air Compressor Market Statistics
- Global Industrial Air Compressor Market Statistics
- Basic Statistics About Compressor Air
- Compressor Air Performance Metrics and Statistics
- Efficiency and Energy Consumption of Air Compressor Statistics
- Cost-effectiveness of Air Compressor Statistics
- Air Conditioner – Applicant of Air Compressor Statistics
- Recent Developments
- Conclusion
- FAQs
Introduction
Air Compressor Statistics: An air compressor is a machine that transforms power into stored potential energy in compressed air.
This compressed air serves various roles in different industries, including powering tools, inflating tires, and operating machinery.
Air compressors comprise vital elements, including a motor or engine, compressor pump, tank or receiver, pressure regulator, safety valve, and control valves.
Various types of air compressors, such as reciprocating, rotary screws, centrifugal, scroll, and axial compressors, cater to specific tasks.
They have manufacturing, construction, automotive, HVAC, oil and gas, medical, and aerospace applications. Making them indispensable instruments across industrial and commercial sectors.
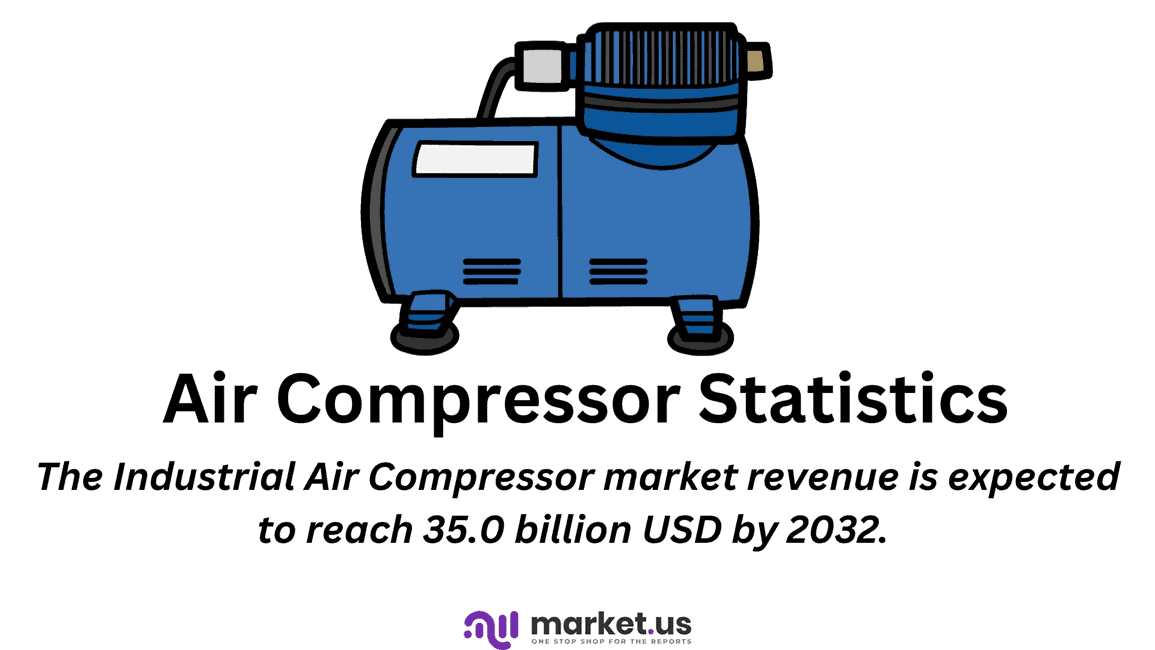
Editor’s Choice
- The worldwide air compressor market was valued at USD 33,012.6 million in 2021 and is projected to witness a 3.1% compound annual growth rate (CAGR) from 2023 to 2032.
- The industrial air compressors market will reach USD 32.5 billion in 2030.
- Compressed air finds utility across a broad spectrum. With applications ranging from as low as 14 PSI to as high as 6004 PSI (1 to 414 bar). Accommodating flow rates ranging from a mere 3.5 CFM (equivalent to 0.1m3) and beyond.
- Many compressors available at hardware stores and compressor dealers fall within the range of 125 to 175 psi (8.5 – 12 bar) regarding pressure.
- Compressed air systems are significant energy consumers. Gobbling up approximately 10% of all industrial electricity consumption. Totaling around 8.8 terawatt–hours (TWh) annually and resulting in CO2 emissions of 3,100 kilotons (kt) per year.
- The air conditioner market is expected to maintain its growth momentum. With projected revenues of USD 62.8 billion in 2023, USD 67.32 billion in 2024, and USD 71.82 billion in 2025.
- In 2022, the demand for room air conditioners had reached 99.9 million units.
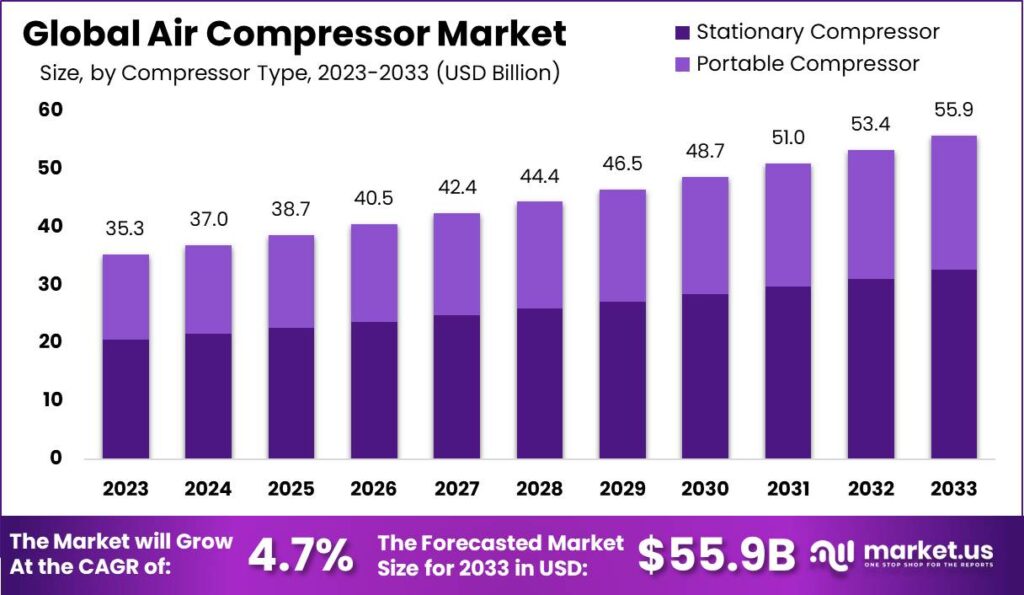
Global Air Compressor Market Statistics
- The worldwide air compressor market was valued at USD 33,012.6 million in 2021 and is projected to witness a 3.1% compound annual growth rate (CAGR) from 2023 to 2032.
- Manufacturing was the dominant sector in 2021.
- The Asia Pacific region accounted for 36.1% of the market share in 2021.
- The market is competitive, with notable industry leaders like AireTex Compressors, Atlas Copco, and BelAire Compressors.
(Source: Market.us)
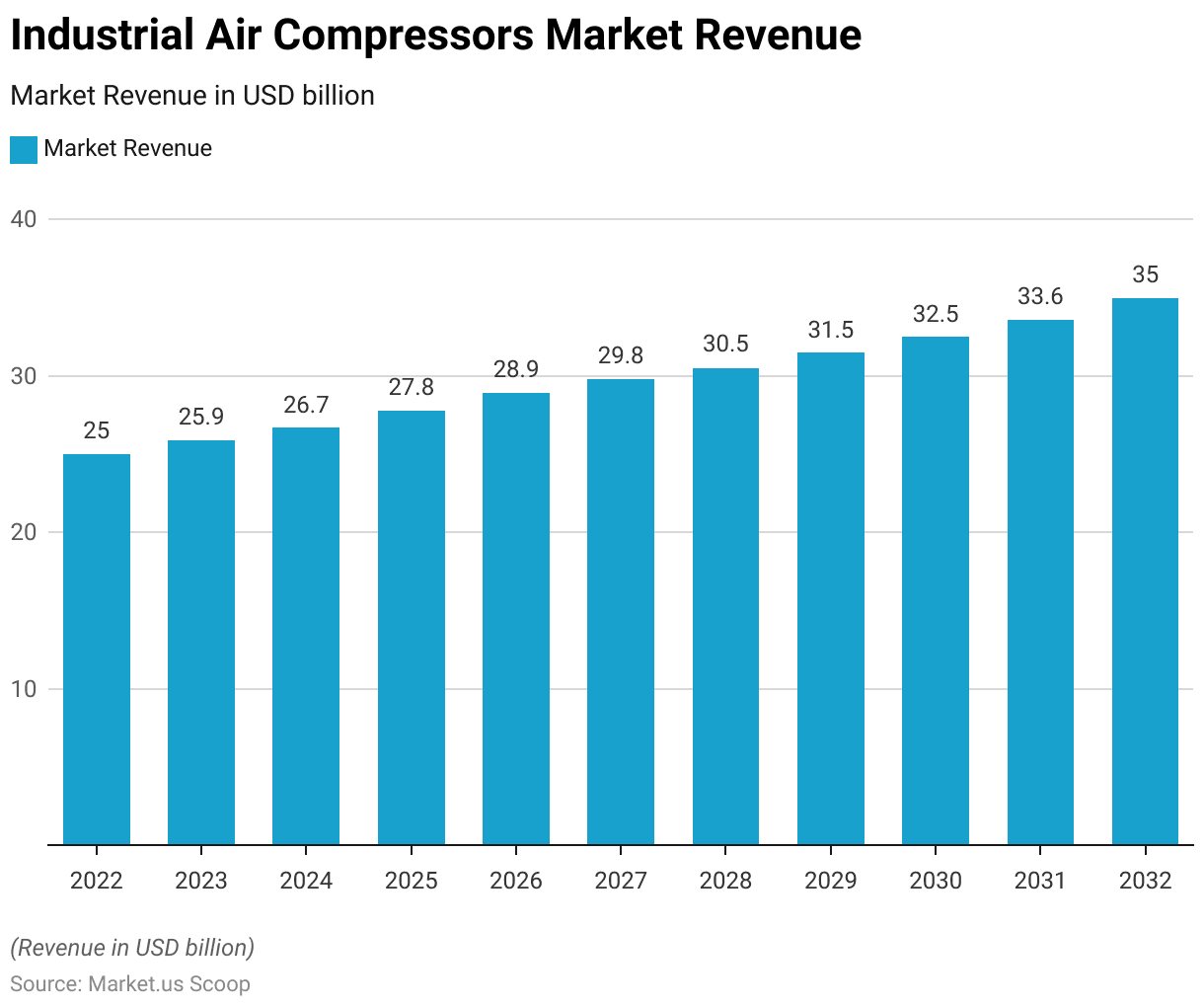
Global Industrial Air Compressor Market Statistics
- Over the next decade, the industrial air compressors market is set to experience a steady and consistent rise in revenue at a CAGR of 3.5%.
- Starting at USD 25.0 billion in 2022, the market’s financial outlook appears promising, with projected figures indicating substantial growth.
- In 2023, revenues are expected to reach USD 25.9 billion. Followed by USD 26.7 billion in 2024 and USD 27.8 billion in 2025.
- This upward trajectory continues throughout the forecast period. With revenues increasing to USD 28.9 billion in 2026, USD 29.8 billion in 2027, and USD 30.5 billion in 2028.
- By 2029, the market is predicted to surpass USD 31.5 billion, further strengthening its position.
- As we progress into the 2030s, the industrial air compressors market is anticipated to reach USD 32.5 billion in 2030, and by 2032. It is expected to achieve an impressive milestone of USD 35.0 billion.
- This growth can be attributed to several factors, including the increasing demand for compressed air systems across various industries, and industrial automation. The pursuit of energy-efficient solutions, and continuous advancements in compressor technology.
- The future of the industrial air compressors market seems promising, characterized by a consistent upward trajectory in revenue.
(Source: MarketResearch.biz)
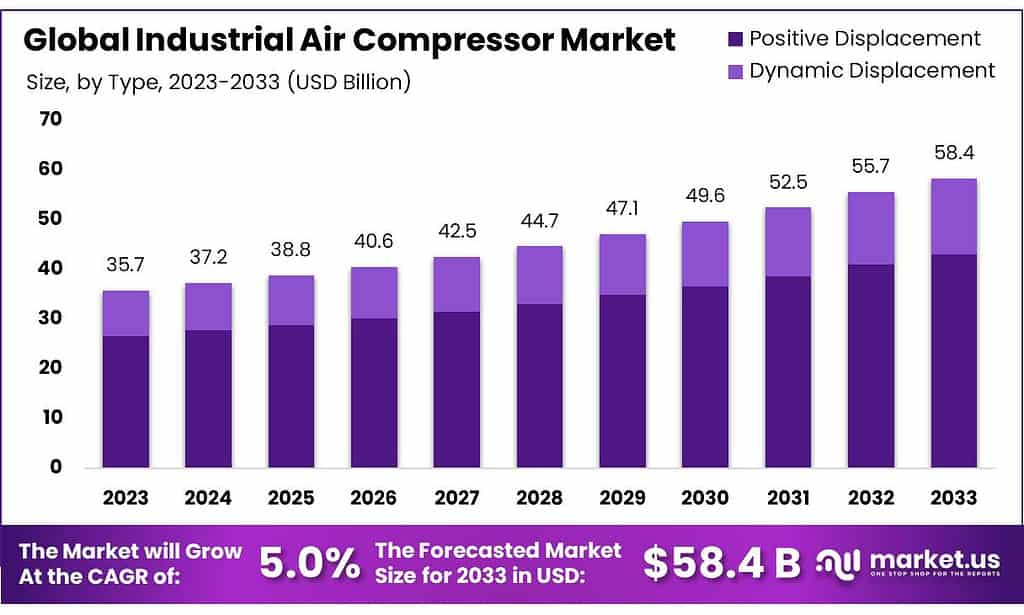
Basic Statistics About Compressor Air
- Atmospheric and compressed air are similar, comprising approximately 78% nitrogen, 20-21% oxygen, and around 1-2% water vapor, carbon dioxide, and other trace gases.
- Compressed air finds utility across a broad spectrum, with applications ranging from as low as 14 PSI to as high as 6004 PSI (1 to 414 bar). Accommodating flow rates ranging from a mere 3.5 CFM (equivalent to 0.1m3) and beyond.
- A typical compressed gas cylinder stands at a height of approximately 4 feet and has a weight ranging from 75 to 80 pounds, including its contents. Which are pressurized to levels as high as 2,200 pounds per square inch (psi).
(Source: VMAC, SafetyNow ILT)
Compressor Air Performance Metrics and Statistics
Horsepower
- Horsepower gauges the motor’s effectiveness in an air compressor, considering a specific CFM and PSI. It indicates the machine’s operational capability and is a key attribute to consider when buying.
- A rule of thumb prevails in air compressors: each horsepower roughly equates to an output of about 4 to 5 cubic feet per minute (cfm) of compressed air. Operating at a pressure of 100 pounds per square inch (psi).
- To illustrate, a one-horsepower compressor typically supplies approximately 4 to 5 cfm when working at 100 psi. Whereas a ten-horsepower counterpart can yield roughly 40 to 50 cfm under the same pressure.
- Yet, when the need arises for higher pressure, say 125 psi, this general guideline loses its accuracy. Demanding more horsepower to maintain the same output level.
- Furthermore, an interesting correlation exists: roughly 1 gallon of water is produced for every horsepower generated by a compressor.
- For instance, a 45-horsepower compressor operating at a rate of about seven cubic meters per minute accumulates approximately 23 gallons of water daily. Provided conditions hover around 20 degrees Celsius with 50% relative humidity.
- It’s important to note, however, that not all of this water transitions into liquid form; typically, in a system devoid of an air dryer. Approximately 1/4 condenses into liquid within the aftercooler, and 2/4 within the piping system (given ample time to cool down).
- At the same time, the remaining 1/4 lingers within the compressed air as water vapor.
(Source: Air Compressor Guide)
Pressure (PSI)
- Regarding purchasing an air compressor, two primary specifications take the spotlight: pressure and capacity.
- Pressure is typically measured in units like bar or PSI (pounds per square inch).
- Many compressors available at hardware stores and compressor dealers fall within the range of 125 to 175 psi (8.5 – 12 bar) regarding pressure.
- However, the real differentiator lies in their capacity. The pressure requirement is determined by the specific tools or equipment you plan to use—think, “This nailer needs 100 psi,” or “The machine operates at 125 psi.”
- On the other hand, the required capacity of your air compressor hinges on the collective air consumption of all your tools and machinery. Which may also vary depending on how many you’re operating simultaneously.
- Compressed air equipment is usually engineered to perform optimally at around 90 – 100 psi (6 – 7 bar).
- Hence, most users find that a compressor with a maximum pressure of 7 bar suffices for their needs.
- However, applications such as 15 or 30 bar demand higher pressures, necessitating specialized compressors to meet those specific requirements.
(Source: Air Compressor Guide)
Duty Cycle
- The duty cycle in air compressors relates to how often you can use them within a specific timeframe. For instance, when an air compressor boasts a 100% duty cycle, it can run non-stop without requiring breaks for cooling.
- On the other hand, standard compressors usually come with duty cycles ranging from 50% to 100%.
- This implies that after running for a certain percentage of the time, typically between 50% to 100%. You should turn them off to allow the motor to cool down before using them again.
- This safeguard prevents overheating and ensures the compressor’s longevity and reliable performance.
- Duty cycles are typically expressed in percentages, indicating how much time a compressor is actively working versus how much time it’s at rest.
- For example, if a compressor has a duty cycle of 60/40, it operates for 60% of the time and remains idle or off for 40% of the time.
- This specification is important to understand how continuously a compressor can be used without overheating or experiencing excessive wear.
(Source: NiGen International L.L.C, Air Compressor Guide)
Efficiency and Energy Consumption of Air Compressor Statistics
- Compressed air systems are significant energy consumers, gobbling up approximately 10% of all industrial electricity consumption. Totaling around 8.8 terawatt-hours (TWh) annually and resulting in CO2 emissions of 3,100 kilotons (kt) per year.
- Among these systems, roughly 15% utilize more than one compressor. Contributing to an energy consumption of about 1.3 TWh or 470 kt of CO2 emissions each year.
- These compressed air systems remain in operation continuously for 8,000 hours annually.
- The cost of electricity stands at 11.14 pence per kilowatt-hour (kWh), and the associated carbon emissions for electricity usage are approximately 0.35156 kilograms of CO2 per kWh.
- Meanwhile, the gas price is 2.59 pence per kWh, with carbon emissions for gas usage estimated at 0. If you have a compressor with a 90-kilowatt (kW) capacity that operates at full load, delivering 14.25 cubic meters per minute (m³/min), and runs for a total of 8,000 hours annually. Installing an ETL (Energy Technology List) listed master controller could result in substantial annual savings.
- This reduces energy consumption by about 108 megawatt-hours (MWh) annually.
- Moreover, it could lead to a decrease of approximately 38 metric tonnes of CO2 emissions each year.
(Source: Department for Business, Energy & Industrial Strategy, Government of U.K)
Cost-effectiveness of Air Compressor Statistics
- The realized annual savings for the compressed air system in Dayton, Tennessee, were examined through several recommendations.
- Installing a new compressor system and piping resulted in significant benefits, including energy savings of 292,283 kWh per year, equating to cost savings of $21,980 annually.
- The project incurred a cost of $27,800 and had a simple payback period of 15 months.
- Secondly, by eliminating nitrogen as a backup, an annual cost saving of $8,200 was achieved, with no associated project cost, rendering an immediate payback.
- Lastly, implementing an annual leak detection and repair program led to energy savings of 120,832 kWh per year, translating to cost savings of $9,100.
- The project cost for this recommendation was $2,500, resulting in a rapid payback period of just three months.
- These measures collectively contributed to substantial energy and cost savings, enhancing the efficiency and sustainability of the compressed air system.
(Source: University of Northern Iowa)
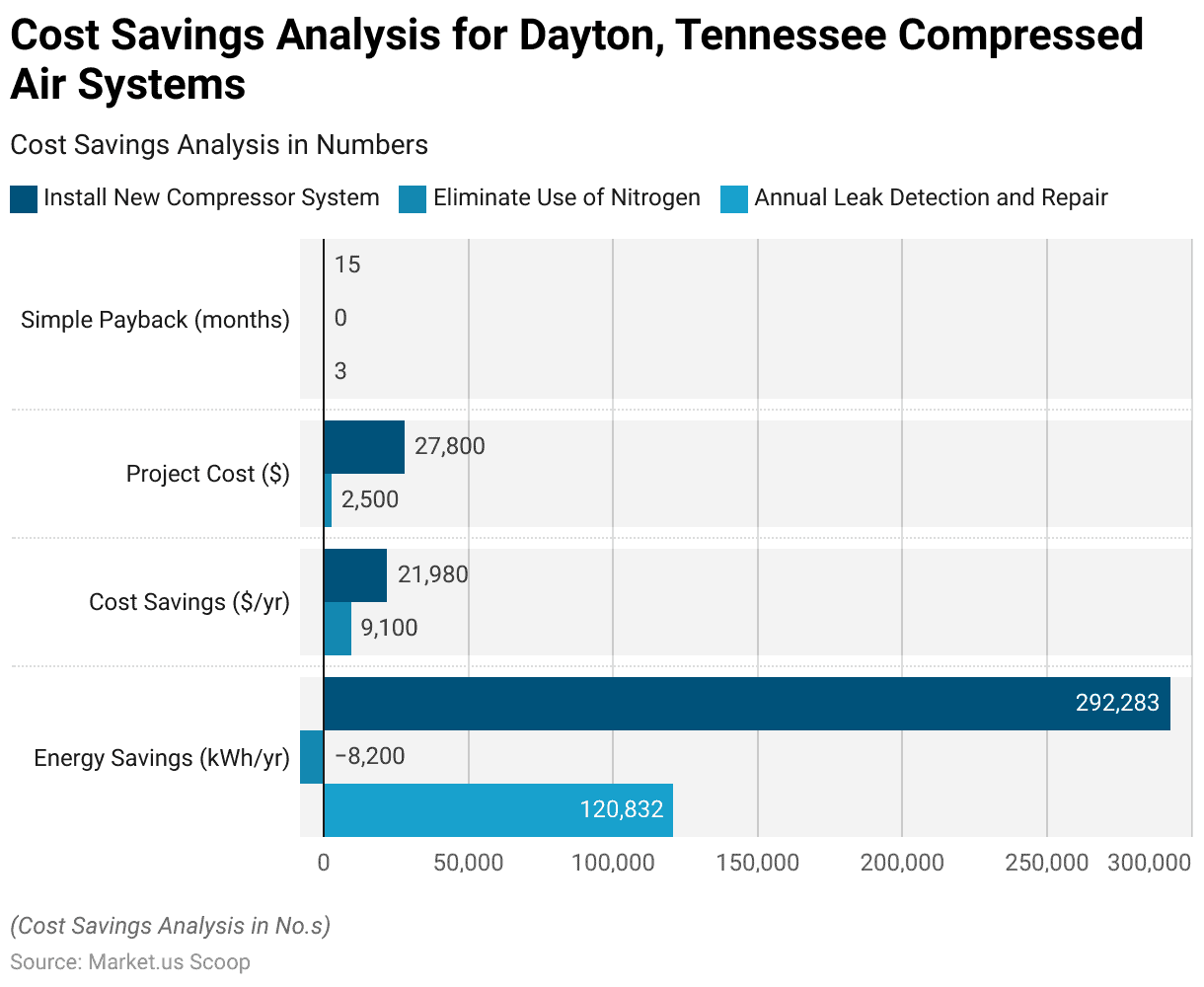
Air Conditioner – Applicant of Air Compressor Statistics
Global Air Conditioner Market Revenue
- The air conditioner systems market has grown steadily in recent years, with its revenue figures reflecting this upward trajectory.
- In 2018, the market recorded a revenue of USD 49.68 billion; by 2019, it had increased to USD 52.11 billion.
- Although there was a slight dip in 2020, with revenue at USD 47.3 billion, the market quickly rebounded in 2021, reaching USD 53.45 billion.
- The growth trend continued in 2022, as the market generated USD 56.81 billion in revenue.
- The air conditioner market is expected to maintain its growth momentum. With projected revenues of USD 62.8 billion in 2023, USD 67.32 billion in 2024, and USD 71.82 billion in 2025.
- The market’s expansion is anticipated to persist. With revenues reaching USD 76.23 billion in 2026, USD 81.2 billion in 2027, and USD 86.36 billion in 2028.
(Source: Statista)
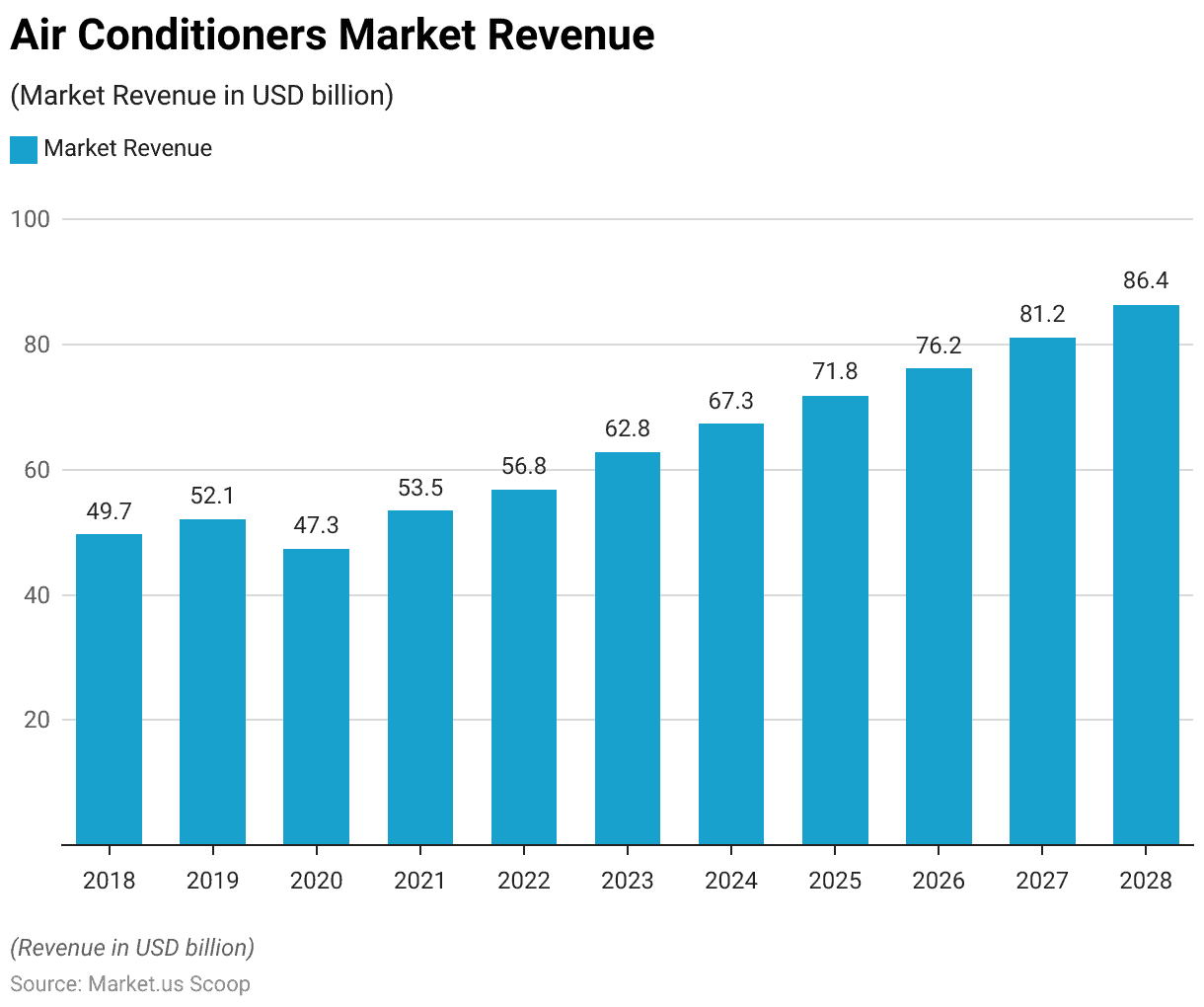
Global Demand for Air Conditioners
- Over the past decade, the global demand for air conditioners has shown a noteworthy trend.
- In 2012, the demand for room air conditioners stood at 85.11 million units, while packaged air conditioner demand was 12.49 million units.
- Over the subsequent years, we witnessed a gradual increase in these numbers. By 2017, the demand for room air conditioners had surged to 96.41 million units, and packaged air conditioner demand reached 14.57 million.
- While slight fluctuations occurred in the following years, 2019 marked a significant milestone, with room air conditioner demand peaking at 101.95 million units.
- However, both types of air conditioners saw a dip in demand in 2020, with room air conditioners at 93.95 million units and packaged air conditioners at 13.5 million.
- The trend then began to recover, and by 2022, the demand for room air conditioners had reached 99.9 million units, while packaged air conditioner demand had surged to 17.87 million units.
- These figures reflect the growing reliance on air conditioning systems worldwide, driven by increasing urbanization and rising temperatures. These have become particularly important for maintaining comfort and productivity in residential and commercial settings.
(Source: Statista)
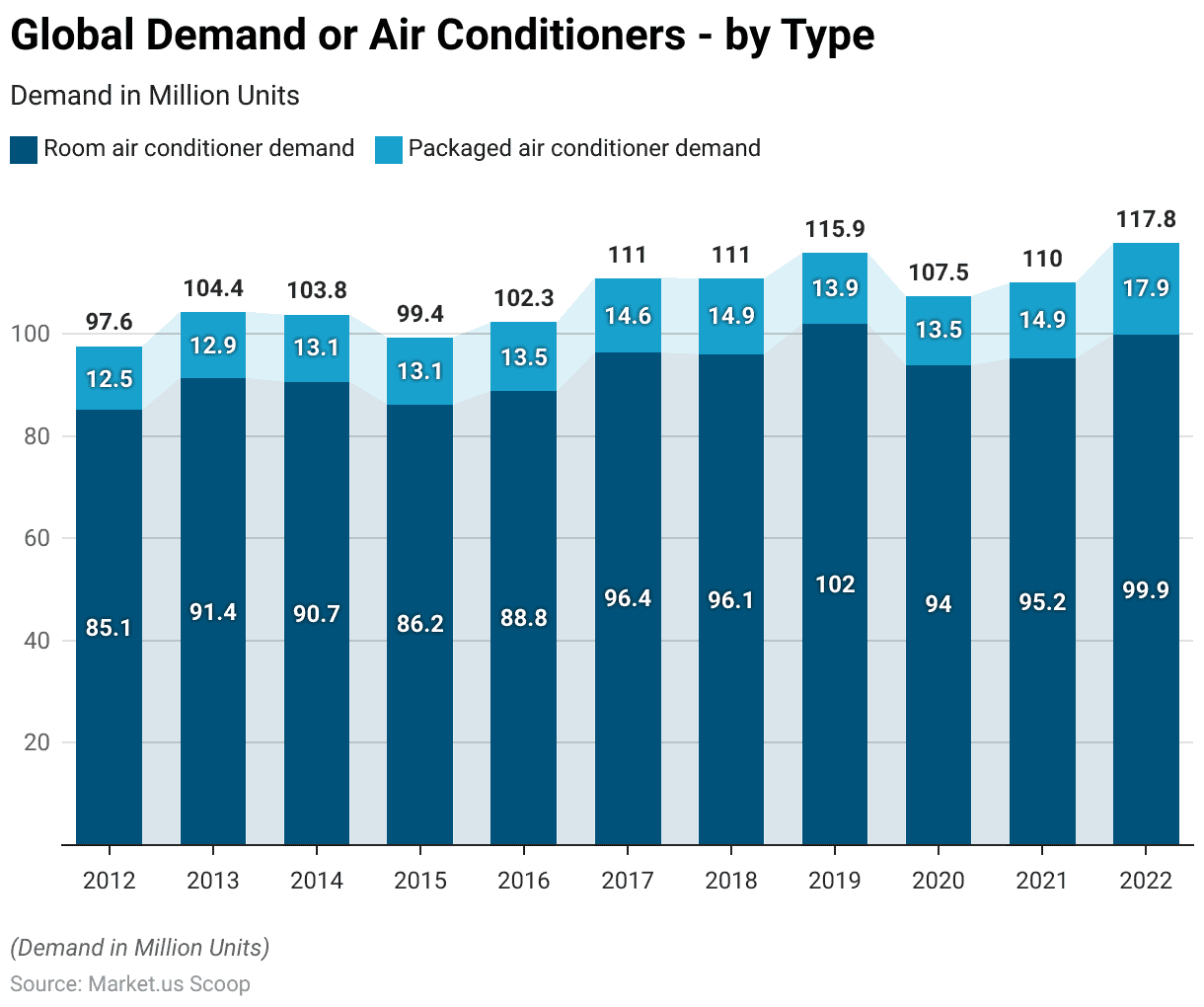
Recent Developments
Acquisitions and Mergers:
- Atlas Copco acquires AirScan: In mid-2023, Atlas Copco acquired AirScan, a company specializing in air compressor monitoring and optimization solutions, for $80 million. This acquisition aims to enhance Atlas Copco’s product offerings with advanced monitoring technologies, improving efficiency and reliability.
- Ingersoll Rand acquires Altec AIR: In late 2023, Ingersoll Rand completed its acquisition of Altec AIR, a provider of air compressors and air treatment solutions, for $90 million. This merger is expected to expand Ingersoll Rand’s portfolio in the compressed air market, particularly in medical and industrial applications.
New Product Launches:
- Kaeser Compressors’ CSG-2 Series: In early 2024, Kaeser Compressors launched the CSG-2 series, a new line of rotary screw air compressors featuring improved energy efficiency. Reduced noise levels, and advanced control systems for optimized performance in industrial settings.
- Sullair’s Next-Generation Portable Air Compressors: Sullair introduced its next-generation portable air compressors in mid-2023, designed for construction and mining applications. These compressors offer enhanced durability, higher air output, and better fuel efficiency.
Funding:
- Gardner Denver secures $100 million: In 2023, Gardner Denver, a leading manufacturer of air compressors, raised $100 million to expand its production facilities and invest in research and development for advanced air compressor technologies.
- Elgi Equipments raises $75 million: Elgi Equipments, a global air compressor manufacturer, secured $75 million in early 2024 to enhance its product development capabilities and expand its market reach, focusing on innovative and energy-efficient solutions.
Technological Advancements:
- AI and IoT Integration: Advances in AI and IoT are being integrated into air compressors to provide real-time monitoring. Predictive maintenance, and energy optimization, leading to improved performance and reduced operational costs.
- Oil-Free Air Compressors: The development of oil-free air compressors is gaining momentum, offering benefits such as reduced maintenance. Improved air quality, and compliance with stringent environmental regulations, making them ideal for food, pharmaceutical, and electronics industries.
Market Dynamics:
- Growth in the Air Compressor Market: The global air compressor market is projected to grow at a CAGR of 5.6% from 2023 to 2028, driven by increasing demand in manufacturing, automotive, and construction sectors, as well as the need for energy-efficient solutions.
- Rising Demand in Asia-Pacific: The Asia-Pacific region is seeing significant growth in the air compressor market due to rapid industrialization, urbanization, and infrastructure development, particularly in countries like China and India.
Regulatory and Strategic Developments:
- EU Ecodesign Directive: The European Union updated its Ecodesign Directive in early 2024, setting stricter energy efficiency standards for air compressors. This regulation aims to reduce energy consumption and promote the development of more sustainable air compressor technologies.
- US DOE Energy Efficiency Standards: The US Department of Energy (DOE) implemented new energy efficiency standards for air compressors in 2023. Requiring manufacturers to meet higher efficiency benchmarks to reduce energy use and environmental impact.
Research and Development:
- Advanced Compressor Materials: R&D efforts are focusing on developing advanced materials such as composites and high-strength alloys to improve the durability, efficiency, and performance of air compressors, reducing weight and maintenance needs.
- Noise Reduction Technologies: Researchers are working on noise reduction technologies for air compressors. Aiming to develop quieter systems that are suitable for use in noise-sensitive environments like hospitals and laboratories.
Conclusion
Air Compressor Statistics – Air compressors are essential tools used across industries, converting power into compressed air for many tasks.
The choice of the right compressor depends on factors like pressure and capacity, matching the tools’ needs. Understanding the duty cycle is vital to maintaining a compressor’s performance.
However, they can consume significant energy, contributing to CO2 emissions, so energy-efficient options and practices are crucial.
Air compressors play a pivotal role in various sectors, and selecting them wisely while focusing on efficiency is key to productivity and sustainability.
FAQs
An air compressor is a mechanical device that converts power into compressed air, which can be used for various purposes, such as powering tools, inflating tires, and operating machinery.
Common types of air compressors include reciprocating, rotary screw, centrifugal, scroll, and axial compressors, each suited for specific applications.
The duty cycle indicates how frequently an air compressor can run without overheating. It’s often expressed as a percentage and is essential for the compressor’s longevity.
Air compressors can be significant energy consumers, so it’s essential to consider energy-efficient options and practices to reduce their environmental impact and operating costs.
The lifespan of an air compressor can vary depending on usage, maintenance, and the compressor’s quality. Many air compressors can last 10-15 years or more with proper care.
Discuss your needs with our analyst
Please share your requirements with more details so our analyst can check if they can solve your problem(s)
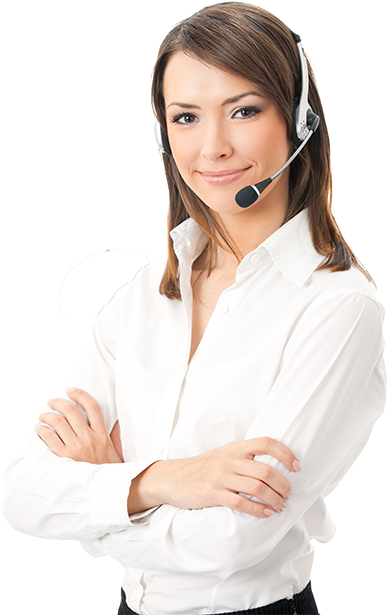