Table of Contents
- Introduction
- Editor’s Choice
- Aerospace and Defense Industry Statistics
- Materials Used in Aircraft Design
- Aerospace Plastics Market Statistics
- BASF Aerospace Plastics Statistics
- Hyosung Aerospace Plastics Statistics
- Mitsubishi Aerospace Plastics Statistics
- Evonik Aerospace Plastics Statistics
- SGL Carbon SE Aerospace Plastics Statistics
- Celanese Aerospace Plastics Statistics
- Solvay Aerospace Plastics Statistics
- Victrex Aerospace Plastics Statistics
- Ensinger Aerospace Plastics Statistics
- PPG Industries Aerospace Plastics Statistics
- Single-use Plastics for Aviation
- Regulations for Single-use Plastics in Aviation
- Key Investments
- Regulations for Aerospace Plastics
- Innovations and Developments in Aerospace Plastics Statistics
- Recent Developments
- Conclusion
- FAQs
Introduction
Aerospace Plastics Statistics: Aerospace plastics are specialized materials designed for the aerospace industry. Known for their lightweight strength, durability, and resistance to environmental factors.
They include thermoplastics like Polyether Ether Ketone (PEEK) and Polyimide, as well as thermosetting plastics like epoxy and phenolic resins.
These materials are utilized in various applications, including structural components, interiors, electrical insulation, and fuel systems. Contributing to weight reduction and enhanced fuel efficiency in aircraft.
Manufacturing processes such as injection molding and 3D printing facilitate the production of complex shapes with high precision.
Compliance with strict regulatory standards ensures safety and reliability. Ongoing advancements in composite materials and sustainable plastics are shaping the future of aerospace technology.
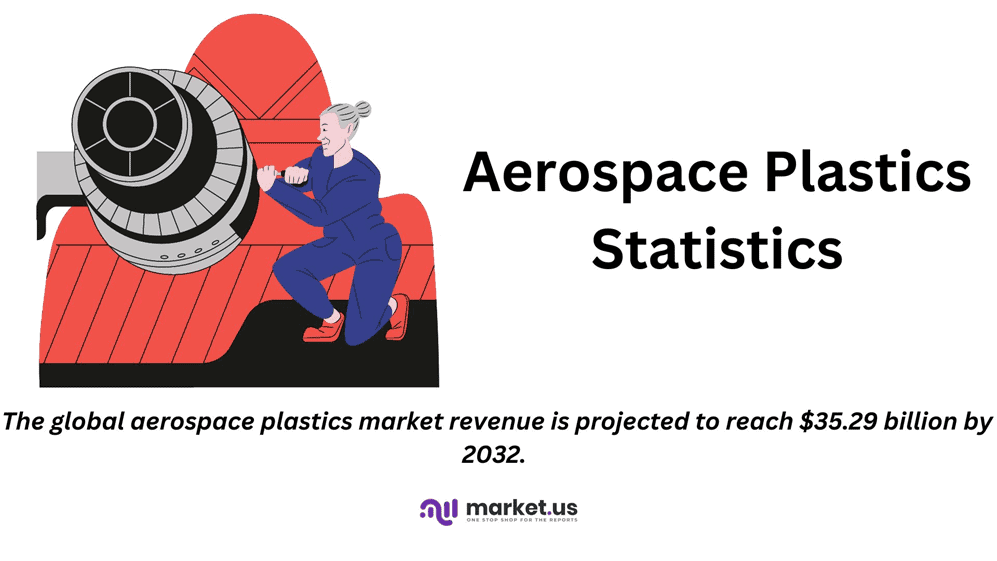
Editor’s Choice
- The global aerospace plastics market revenue is projected to reach $35.29 billion by 2032.
- The competitive landscape of the global aerospace plastics market is characterized by a diverse array of key players, each holding a significant market share. Hyosung Corporation leads with an 18% share.
- The global distribution of market shares in the aerospace plastics sector illustrates a significant concentration of activity across various regions. North America leads with a dominant 42.0% of the market share, underscoring its pivotal role in the aerospace industry.
- A 2023 IATA passenger survey indicated that over three-quarters of passengers would prefer a flight without SUPP, even if it meant fewer food and beverage options.
- In 2022, global research and development (R&D) spending on aerospace and defense amounted to a total of 21.4 billion euros.
- The United Nations has initiated efforts towards a legally binding global plastics treaty. Aiming to address the lifecycle impacts of plastics, including those used in aerospace.
- Companies like SABIC and Victrex are at the forefront of developing advanced plastic composites that are increasingly replacing metals in aerospace applications due to their advantageous weight-to-strength ratio.
Aerospace and Defense Industry Statistics
Global Aerospace and Defense Industry Revenue
- The global aerospace and defense industry has exhibited fluctuating revenue patterns from 2019 through 2023.
- In 2019, the industry generated $754 billion.
- The following year, 2020, saw a decline in revenue to $681 billion, likely influenced by global disruptions.
- A gradual recovery was observed in 2021, with revenue increasing to $714 billion.
- The upward trend continued into 2022, with revenues rising to $745 billion.
- By 2023, the industry’s revenue had significantly rebounded to $829 billion, indicating a robust recovery and growth phase.
- This trajectory reflects the dynamic economic conditions impacting the sector over these five years.
(Source: Statista)
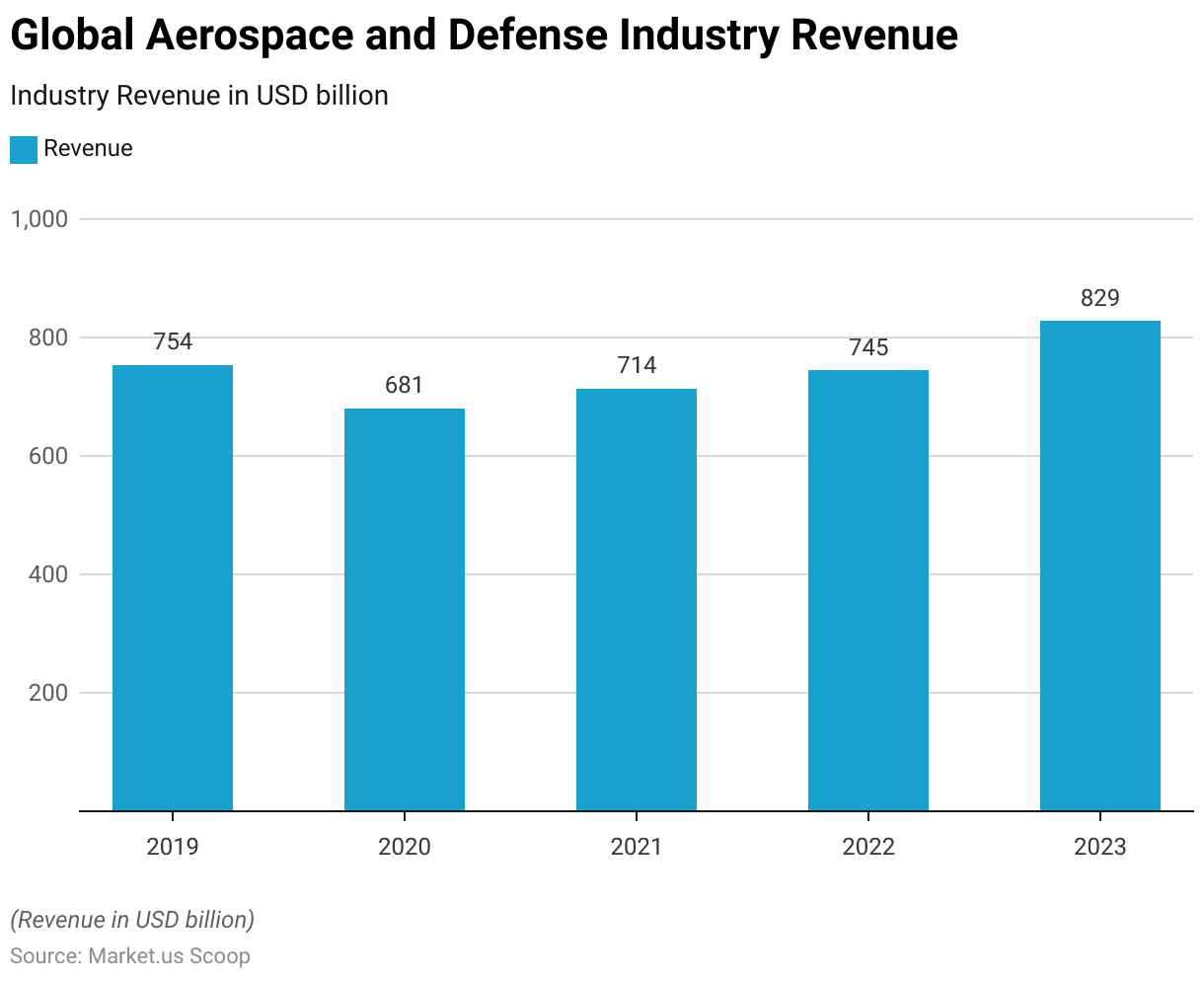
Global Aerospace Coatings Market Size
- The market size for aerospace coatings worldwide stood at $1.99 billion in 2022.
- It is forecasted to experience considerable growth, reaching $3.21 billion by the year 2029.
- This projection suggests a robust expansion in the aerospace coatings sector over the next seven years. Driven by increasing demands for durable and efficient coatings in the aerospace industry.
(Source: Statista)
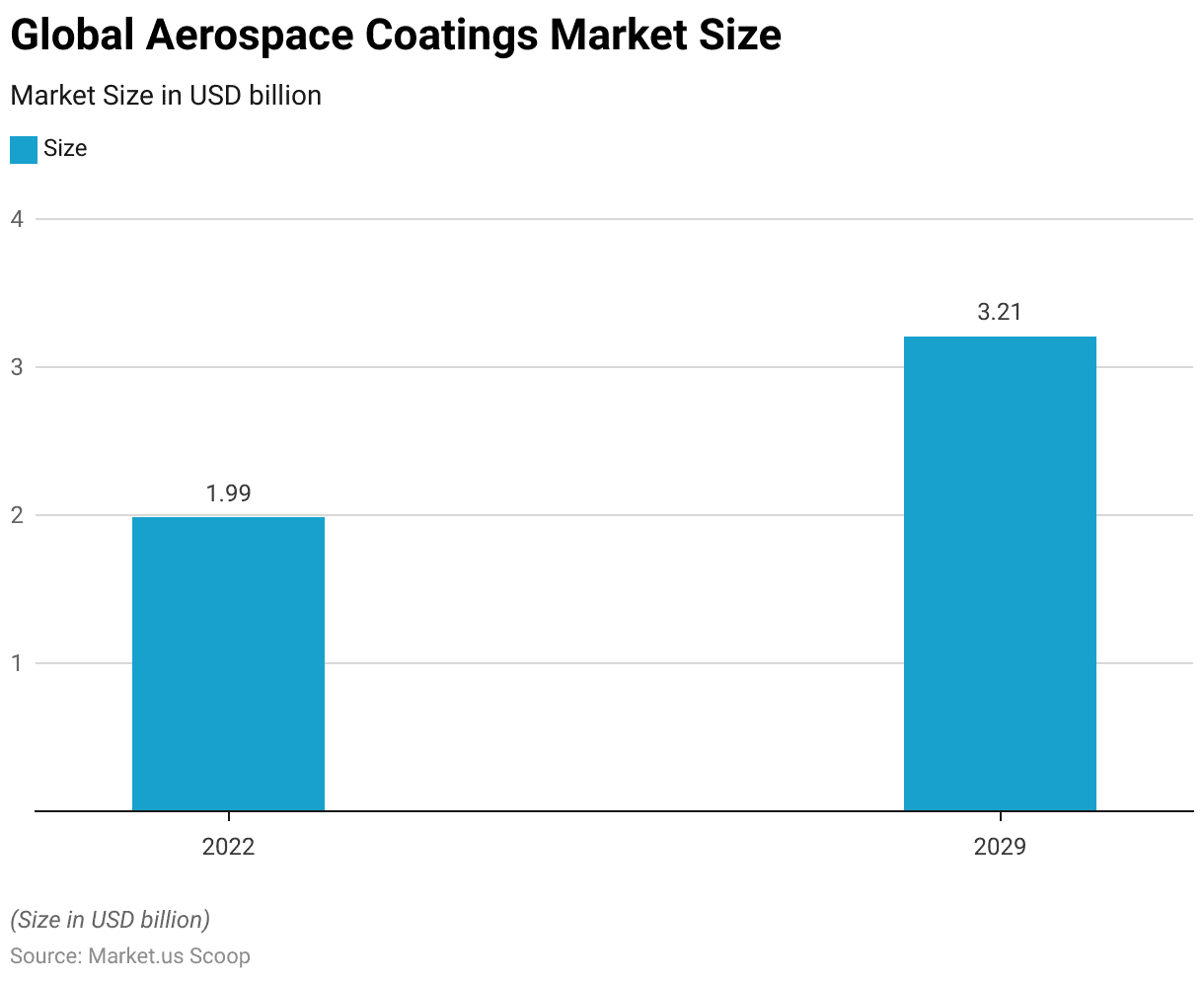
Aerospace Services Market Size – By Region
- The projected market size of the global aerospace services from 2024 to 2043 by region illustrates a significant disparity in regional market capacities.
- Eurasia leads with a substantial market size of $1,065 billion, followed closely by North America with $1,000 billion.
- China also holds a considerable portion of the market, projected at $780 billion.
- The Middle East and Southeast Asia are expected to have market sizes of $390 billion and $365 billion, respectively.
- Latin America’s market is forecasted at $235 billion, while Northeast Asia’s market size is projected at $190 billion.
- South Asia, Africa, and Oceania round out the list with market sizes of $175 billion, $120 billion, and $80 billion, respectively.
- This distribution indicates diverse growth and investment opportunities across different global regions in the aerospace services sector.
(Source: Statista)
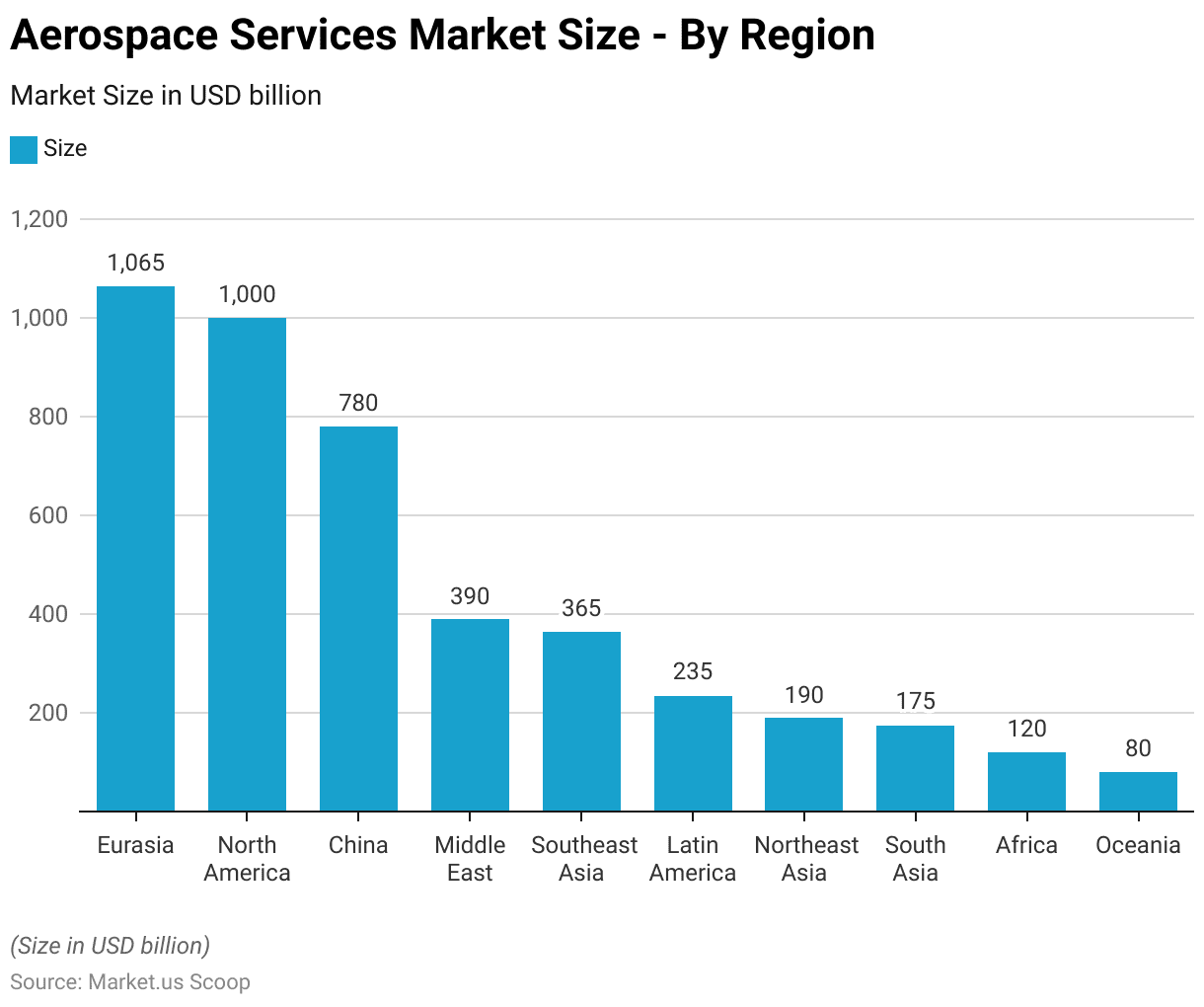
Materials Used in Aircraft Design
- The distribution of composite materials used in commercial aircraft manufacturing has evolved significantly from 1985 to 2014.
- In 1985, aluminum was the predominant material, constituting 74% of the materials used, with steel at 8%, titanium at 5%, composites at 6%, and other materials at 7%.
- By 1987, aluminum usage had decreased to 66%, while composites nearly tripled to 15%.
- The trend continued in 1992, with aluminum steady at 66% and composites increasing slightly to 16%.
- By 2007, aluminum’s share dropped to 61%, and composites rose to 22%.
- A dramatic shift occurred by 2014 when aluminum drastically reduced to 20%. While composites surged to 52%, becoming the majority material.
- Additionally, titanium saw a significant increase to 14% by 2014, with steel at 7% and other materials remaining consistent at around 7%.
- This shift underscores a major transition towards lighter and more efficient composite materials in aircraft manufacturing over nearly three decades.
(Source: Statista)
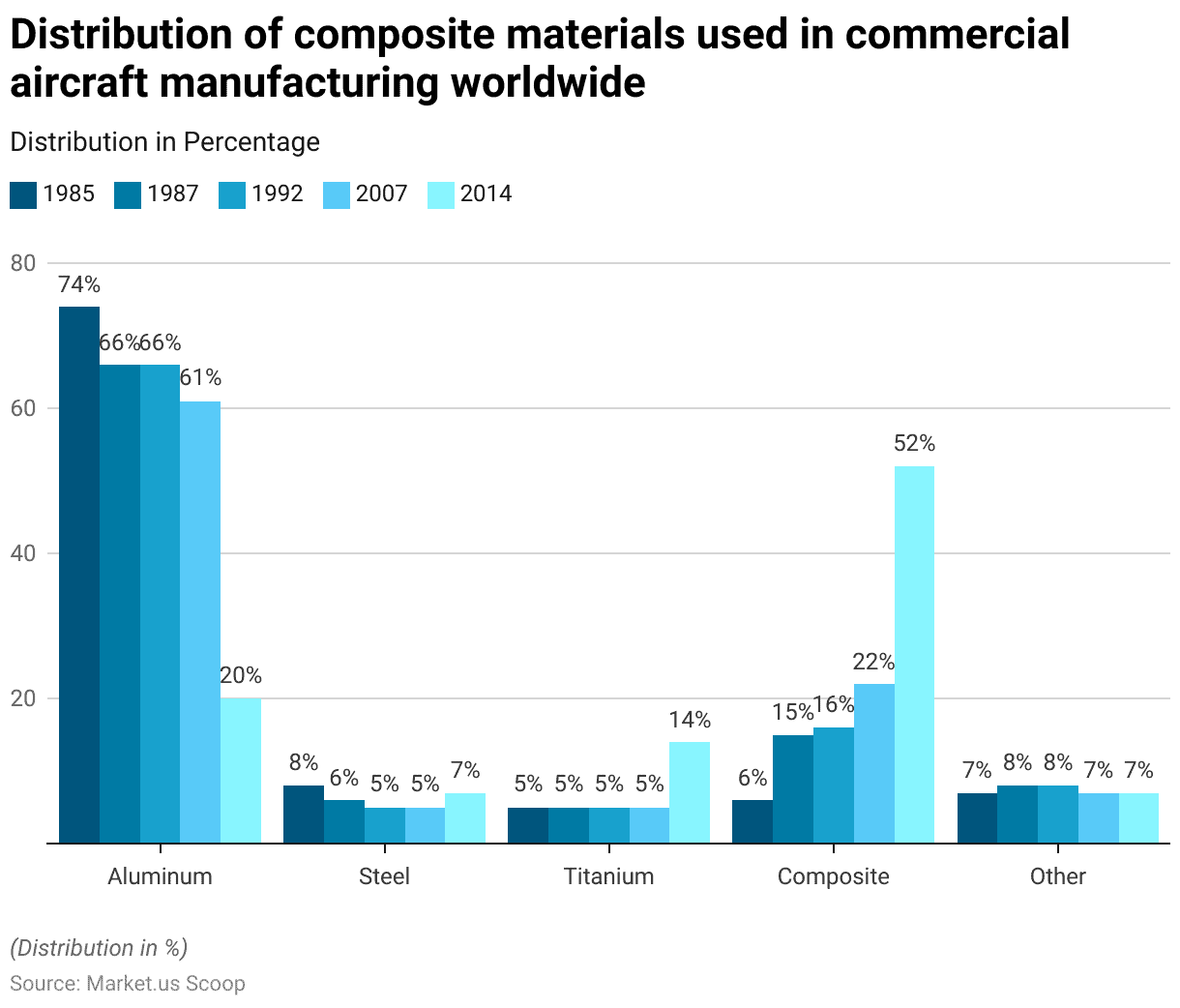
Aerospace Plastics Market Statistics
Global Aerospace Plastics Market Size Statistics
- The global aerospace plastics market has been projected to experience a consistent growth trajectory from 2021 to 2032.
- Starting at $16.77 billion in 2021, the market size increased to $17.94 billion in 2022 and further rose to $19.19 billion in 2023.
- The upward trend is expected to continue, with market sizes projected to reach $20.54 billion in 2024, $21.98 billion in 2025, and $23.51 billion in 2026.
- By 2027, the market is anticipated to grow to $25.16 billion. Followed by $26.92 billion in 2028 and $28.81 billion in 2029.
- The growth momentum is forecasted to sustain into the next decade, with the market expanding to $30.82 billion in 2030, $32.98 billion in 2031, and finally reaching $35.29 billion by 2032.
- This steady increase underscores the expanding utilization of aerospace plastics in the industry. Driven by their advantageous properties and increasing applications in aerospace design and manufacturing.
(Source: market.us)
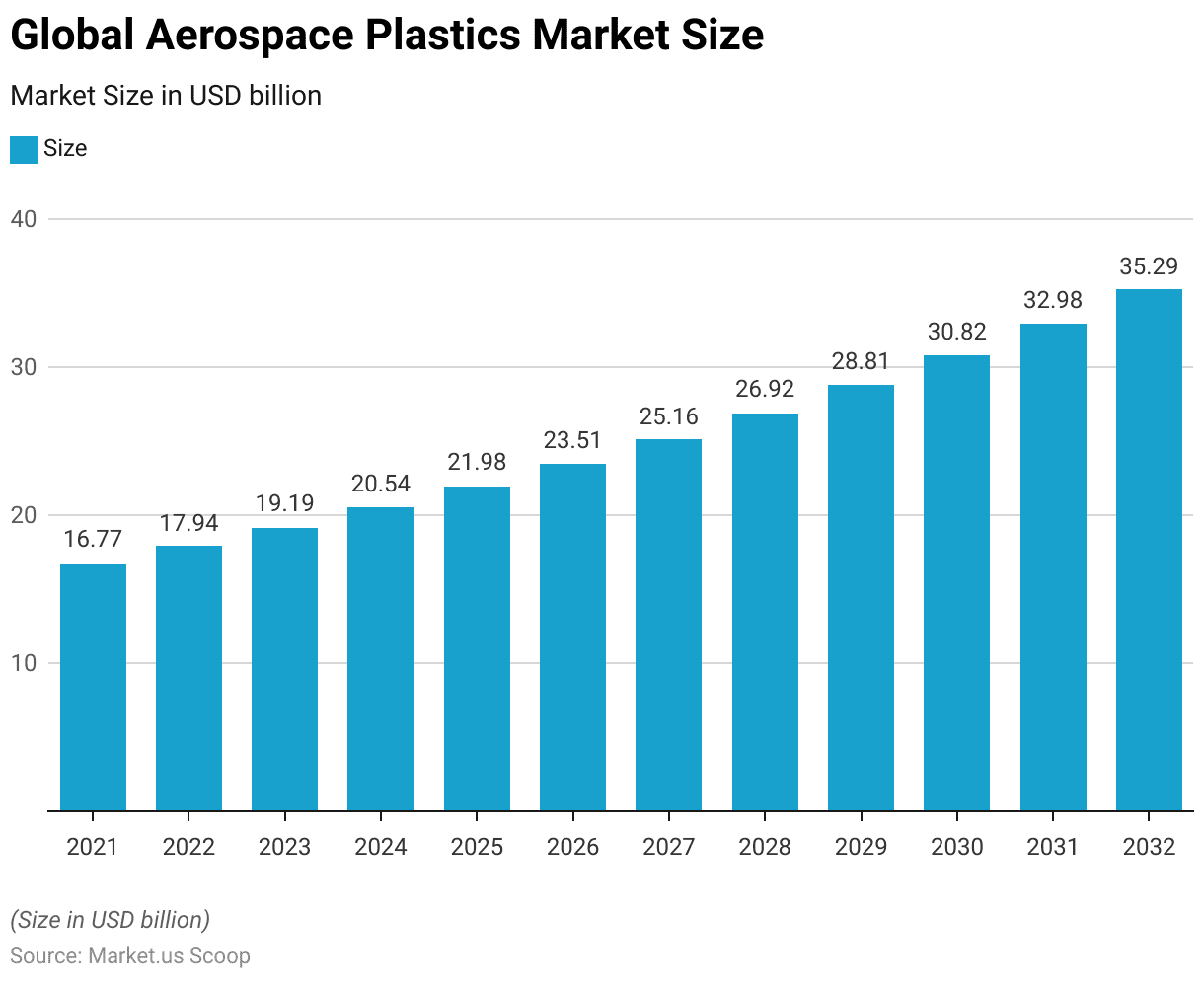
Competitive Landscape of Global Aerospace Plastics Market Statistics
- The competitive landscape of the global aerospace plastics market is characterized by a diverse array of key players, each holding a significant market share.
- Hyosung Corporation leads with an 18% share, closely followed by BASF SE, which commands a 17% market share.
- Other notable companies include Premium Aerotec GmbH, with a 12% share and an aggregated 12% held by various other key players.
- Kaman Corporation contributes 10% to the market, while Mitsubishi Heavy Industries Limited holds 9%.
- SGL Carbon SE and Tech-Tool Plastics Inc. each account for 8% of the market. Evonik Industries AG holds the smallest share among the highlighted companies at 6%.
- This distribution underscores a competitive and fragmented market environment where numerous players vie for leadership and innovation in aerospace plastics.
(Source: market.us)
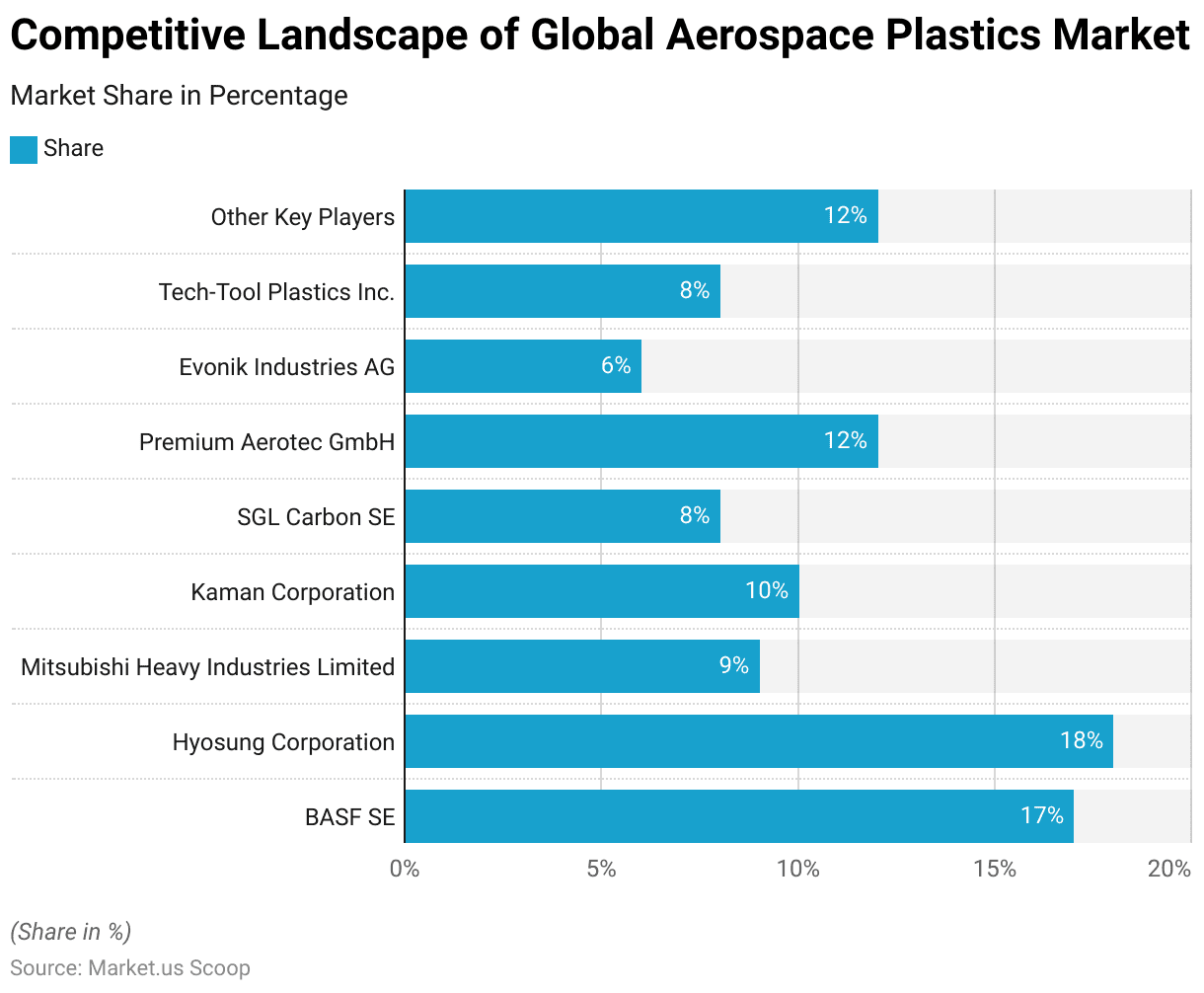
Global Aerospace Plastics Market Share – By Region Statistics
- The global distribution of market shares in the aerospace plastics sector illustrates a significant concentration of activity across various regions.
- North America leads with a dominant 42.0% of the market share, underscoring its pivotal role in the aerospace industry.
- Following North America, the Asia-Pacific (APAC) region holds a substantial 25.0% of the market. Indicating robust growth and investment in aerospace technologies.
- Europe also maintains a strong presence with 22.0% of the market share, reflecting its advanced manufacturing capabilities and technological innovation.
- South America, the Middle East, and Africa (MEA) represent smaller portions of the market, with 7.0% and 4.0%, respectively. Highlighting emerging involvement and potential growth areas within the aerospace plastics industry.
(Source: market.us)
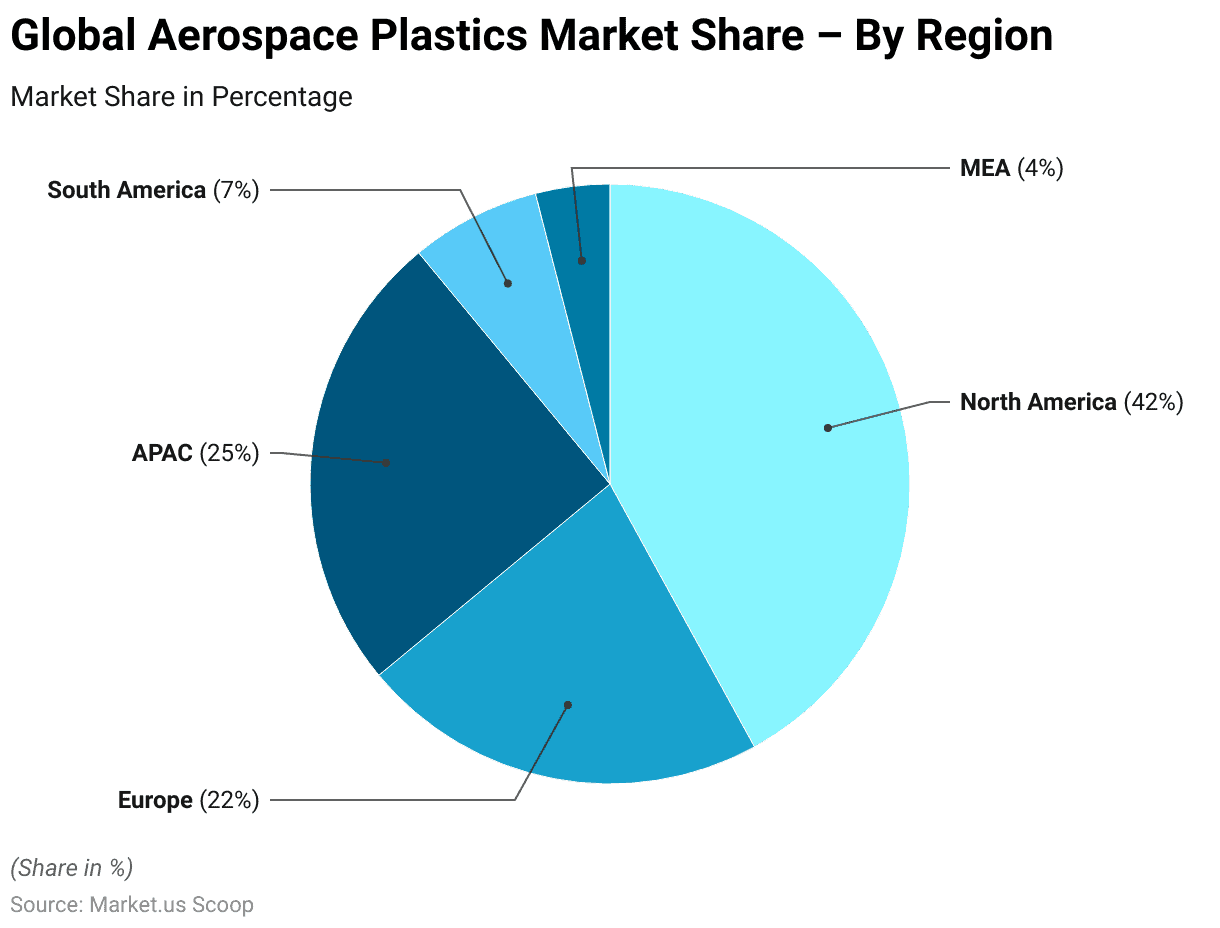
BASF Aerospace Plastics Statistics
- BASF is actively innovating in the aerospace plastics sector, focusing on secondary structural materials and additive manufacturing.
- Their offerings include Ultrason polyethersulfones, which are used to make lightweight, recyclable components like tray tables and seat backs, substituting traditional metals.
- Carbon fiber-reinforced parts complement these thermoplastic composites for high-strength applications.
- Additionally, BASF’s structural polyurethane (PU) foam significantly reduces weight while maintaining structural integrity. Exemplified by their prototype sandwich panel floor that is 40% lighter than aluminum yet supports a 4,200 psi load.
- In additive manufacturing, BASF partners to deliver engineering plastic filaments for fused filament fabrication (FFF), with materials such as Ultrason PESU and Ultramid PA providing enhanced Z strength and EMI shielding.
- They are also developing six polyamide sintering powders for selective laser sintering (SLS), although these are not yet FST-compliant for aerospace. Moreover, their stainless steel 316L-filled filament targets cost-effective 3D-printed metal parts.
- BASF’s collaboration with HP in the Open Materials Platform furthers their development of sintering powders. Their photopolymer technologies are enhancing stereolithography and jetting applications with higher impact strengths and competitive heat deflection temperatures.
(Source: BASF)
Hyosung Aerospace Plastics Statistics
- Hyosung Advanced Materials Corp., headquartered in Seoul, South Korea, is actively advancing sustainable practices and innovative products in the plastics and materials sector.
- They produce Polyketone (POKETONE), an environmentally friendly plastic made from carbon monoxide, ethylene, and propylene. This production process not only utilizes these potentially polluting gases but also reduces environmental pollution.
- Additionally, Hyosung promotes recycling through its production of PCR (Post-Consumer Recycled material) PP and PCR-PET FILM, further enhancing the sustainability of its operations.
- Their polypropylene brand, PP/DH PU, offers high-quality homopolymer, block copolymer, and random copolymer using HYPOL, UNIPOL, and SPHERIPOL processes, catering to a diverse range of applications and markets including China, Japan, Southeast Asia, the Middle East, Europe, and Korea.
- In its pursuit of customer satisfaction, the company focuses on product development and customer services.
- Moreover, in 2018, Hyosung’s Carbon Fiber Business Division launched a new carbon fiber designed for primary and secondary aerospace structures.
- This new fiber, initially available in 24k tow format with 6k and 12k tows to follow, features higher tensile strength and modulus than existing products in the intermediate modulus range. Highlighting Hyosung’s commitment to technological innovation and market leadership.
(Sources: Hyosung Chemicals, Composite World)
Mitsubishi Aerospace Plastics Statistics
- Mitsubishi has developed BIOpreg PFA, a new type of prepreg material that serves as an eco-friendly alternative to the phenolic systems usually used in building structural panels for commercial airplanes.
- This material is free from formaldehyde and made using a resin from sugar cane waste. Ensuring it fits seamlessly into existing manufacturing setups without needing new tools.
- BIOpreg PFA is made mostly from bio-based materials—up to 95%—and can be adjusted with additives like flame retardants to meet different requirements. This significantly lowers the environmental impact over its lifetime compared to traditional phenolic resin systems.
- BIOpreg PFA is versatile, working with various reinforcement fibers such as recycled carbon fiber, 7781 glass fabric, and 2×2 twill carbon fabrics, and can be processed using standard methods like vacuum bagging, autoclaving, and hot compression molding.
- This allows it to be shaped into complex parts like sandwich panels using the same production times as older systems.
(Source: Mitsubishi Chemicals)
Evonik Aerospace Plastics Statistics
- Evonik is advancing the aerospace industry with its innovative chemical solutions. Including its legacy in high-test peroxide (HTP) production and sustainable innovations.
- Their product, PROPULSE, a highly concentrated hydrogen peroxide, offers a green propulsion alternative. Breaking down into just water and oxygen and providing high impulse and density for launch vehicles and rockets.
- Additionally, Evonik’s ROHACELL and ROHAFORM foam cores are crucial in creating lightweight, efficient urban air mobility vehicles.
- These foams provide high thermal stability and strong compression resistance, which are vital for durable aerospace composites.
- ROHAFORM is also flame retardant, enhancing safety in line with fire safety standards like FAR 25.853, and supports recyclability, aligning with circular economy goals.
(Source: Evonik)
SGL Carbon SE Aerospace Plastics Statistics
- SGL Carbon SE specializes in the production of aerospace-grade carbon fibers, which are highly refined and consist almost entirely of carbon. each fiber being microscopically small and about eight times thinner than a human hair.
- These fibers are created through a sophisticated high-tech process beginning with polyacrylonitrile (PAN), a white powdery solid known for its hardness, stiffness, and chemical resistance.
- In the initial stage, thin threads are spun from PAN to form a precursor that is wound onto spools.
- Subsequently, these threads undergo a two-stage heat treatment in an oven where they are first oxidized at temperatures between 200 to 300 degrees Celsius and then carbonized at 1200 to 1800 degrees Celsius to achieve a high carbon content and robust strength.
- After undergoing surface treatment and receiving a sizing application, the carbon fibers are finally wound onto spools, ready for various high-performance applications.
(Source: SGL Carbon SE)
Celanese Aerospace Plastics Statistics
- Vamac® Ethylene Acrylic Elastomers (AEM) are designed to be transformed into cured compounds that exhibit superior resistance to high temperatures and robust defense against various automotive fluids.
- Unlike many other heat and oil-resistant polymers, Vamac® AEM stands out for its exceptional low-temperature performance. Comfortably meeting OEM standards at temperatures as low as –40 °C, with potential designs accommodating conditions down to –50 °C.
- This makes Vamac® AEM an ideal choice for applications requiring durability in both extreme heat and cold.
- Celanex® PBT grades come with an ECO-B option that utilizes the mass balance process to incorporate renewable raw materials. Helping customers in industries like Medical or Personal Care meet their sustainability goals.
- These grades can contain up to 40% renewable content and achieve up to a 50% reduction in CO2 footprint by using waste-based feedstocks.
- Additionally, Celanex® uses MIC (Mold-In-Color) Technology, which enhances aesthetics while eliminating the need for pollutive painting and finishing processes, maintaining color integrity even after damage.
- Furthermore, Celanex® offers PBT/PET blends in ECO-R grades, specifically designed for visual applications requiring high-quality surface appearance, containing at least 25% post-consumer recycled PET.
- This approach not only meets stringent industry standards but also supports environmental sustainability.
(Source: Corporation)
Solvay Aerospace Plastics Statistics
- Solvay offers a comprehensive range of aerospace plastics prepregs and resin systems tailored for primary and secondary structure applications.
- The CYCOM® series includes products like 977-2, a toughened epoxy ideal for both structures, available in various forms such as uni-tape and different weaves, requiring three hours of curing at 350°F.
- CYCOM® 5276-1 is another toughened epoxy specific to primary structures, and CYCOM® 5320-1, designed for out-of-autoclave processes, offers a flexible post-cure schedule.
- For high temperature and mechanical needs, CYCOM® 5250-4 uses a BMI system requiring an extended cure time.
- MTM® 45-1, another toughened epoxy, is versatile across multiple glass reinforcements. CYCOM® 970 specializes in producing nonporous structures like honeycomb sandwiches. While AVIMID® S, a non-MDA polyimide, caters to high-temperature applications with a unique cure cycle.
- Additionally, CYCOM® 5575-2 and 5577-1, both modified cyanate esters, are optimized for high temperature and electrical performance suitable for advanced aerospace engineering needs.
(Source: Solvay)
Victrex Aerospace Plastics Statistics
- VICTREX AE 250 is a semi-crystalline polymer belonging to the poly aromatic ether ketone (PAEK) family, with a melting temperature around 40°C lower than PEEK while retaining similar mechanical, physical, and chemical resistance properties.
- Its fast crystallization process allows it to maintain excellent chemical resistance in processed laminates. However additional processes like annealing or re-melting may be needed if cooling occurs too quickly.
- The wider processing window of VICTREX AE 250 enhances press consolidation and forming. In a study, unidirectional carbon fiber reinforced tapes, with 58% fiber volume fraction and 192 g/m² fiber areal weight, were impregnated with 34% of the VICTREX AE 250 polymer.
- Coriolis Composites used slit tapes with precise width tolerances for automated fiber placement, resulting in high-quality, void-free laminates.
(Source: Victrex)
Ensinger Aerospace Plastics Statistics
- Ensinger Aerospace Plastics offers a wide range of high-performance materials suited for various aerospace applications.
- TECASINT 4121 and 2021 (PI) feature low friction and wear with heat distortion temperatures (HDT) up to 470°C. TECASINT 4111 (PI) offers high stiffness and low outgassing in a vacuum. While TECASINT 2391 (PI) is modified with MoS2 for optimal gliding properties in vacuum environments.
- TECASINT 2011 natural (PI) provides maximum strength, excellent electrical insulation, and low thermal conductivity.
- TECAPEEK natural (PEEK) excels in long-term service at temperatures up to 260°C. While TECAPEEK CF30 and GF30 are reinforced with carbon fiber and glass fiber, respectively, for increased strength and abrasion resistance. TECAPEEK ELS nano (PEEK CNT) adds electrical conductivity and machinability.
- TECATRON GF40 (PPS GF) combines glass-fiber reinforcement with excellent chemical resistance, and TECASON P (PPSU) provides high thermal stability. TECAPEI natural (PEI) withstands long-term temperatures up to 170°C and resists high-energy radiation.
- TECAFLON PTFE offers exceptional chemical resistance and low friction, which is ideal for soft mating partners. TECAMID 66 and its variants (natural, MO, GF) feature strong machinability, UV resistance, and strength.
- TECAFORM materials (POM-C, POM-H) deliver good chemical resistance, resilience, and specialized properties such as conductivity, anti-static features, and slide friction capabilities, making them well-suited for diverse aerospace applications.
(Source: Ensinger)
PPG Industries Aerospace Plastics Statistics
- PPG Industries provides a wide variety of aerospace coatings. Offering over a thousand different types designed for use on materials like fiberglass, composites, and metals. These products meet the standards for Commercial, General Aviation, Military, and AMS applications.
- The Desothane® HS and Desothane® HD topcoats are known for their great appearance, strong durability, and easy application. PPG also offers a range of military and commercial products, including primers, chrome-free coatings, water-based products, pretreatments, and topcoats.
- Their Desoprime™ primers are available in chrome-free, low VOC, and water-reducible versions.
- The Aerocron™ electrocoat process helps reduce waste by 80%, lowers weight by 60%, and improves material usage efficiency to 95%.
- PPG’s strippable intermediate coating can cut repair times by 40%.
- Additionally, their Solar Heat Management coatings help minimize heat absorption, improving the performance of composite structures and reducing cooling requirements.
- For unique livery designs, PPG offers mica and metallic pigments to create distinct styles.
(Source: PPG Industries)
Single-use Plastics for Aviation
- Single-use plastic products (SUPP) have long been integral to the aviation industry due to their lightweight and hygienic benefits. Playing a significant role in both passenger experience and cargo operations.
- However, growing environmental concerns have brought SUPP usage under scrutiny.
- Cabin waste audits from 2013 to 2018 revealed that plastic comprised 17%–20% of waste by weight, though PET bottles, a common SUPP, only made up 2%.
- Civil aviation regulations also mandate the use of some SUPP for safety and security purposes.
- Despite these challenges, around 40 airlines have initiated SUPP reduction and replacement programs, some beginning as early as 2018, although the pandemic temporarily reversed this trend.
- A 2023 IATA passenger survey indicated that over three-quarters of passengers would prefer a flight without SUPP, even if it meant fewer food and beverage options.
- Cargo operators are also facing pressure from customers to reduce plastic packaging. Prompting the introduction of sustainable solutions, though such efforts are still limited.
- The 2022 IATA Shipper Survey found that 50% of cargo customers prioritize waste reduction in the supply chain, with over a third seeking sustainable packaging options.
(Source: International Air Transport Association (IATA))
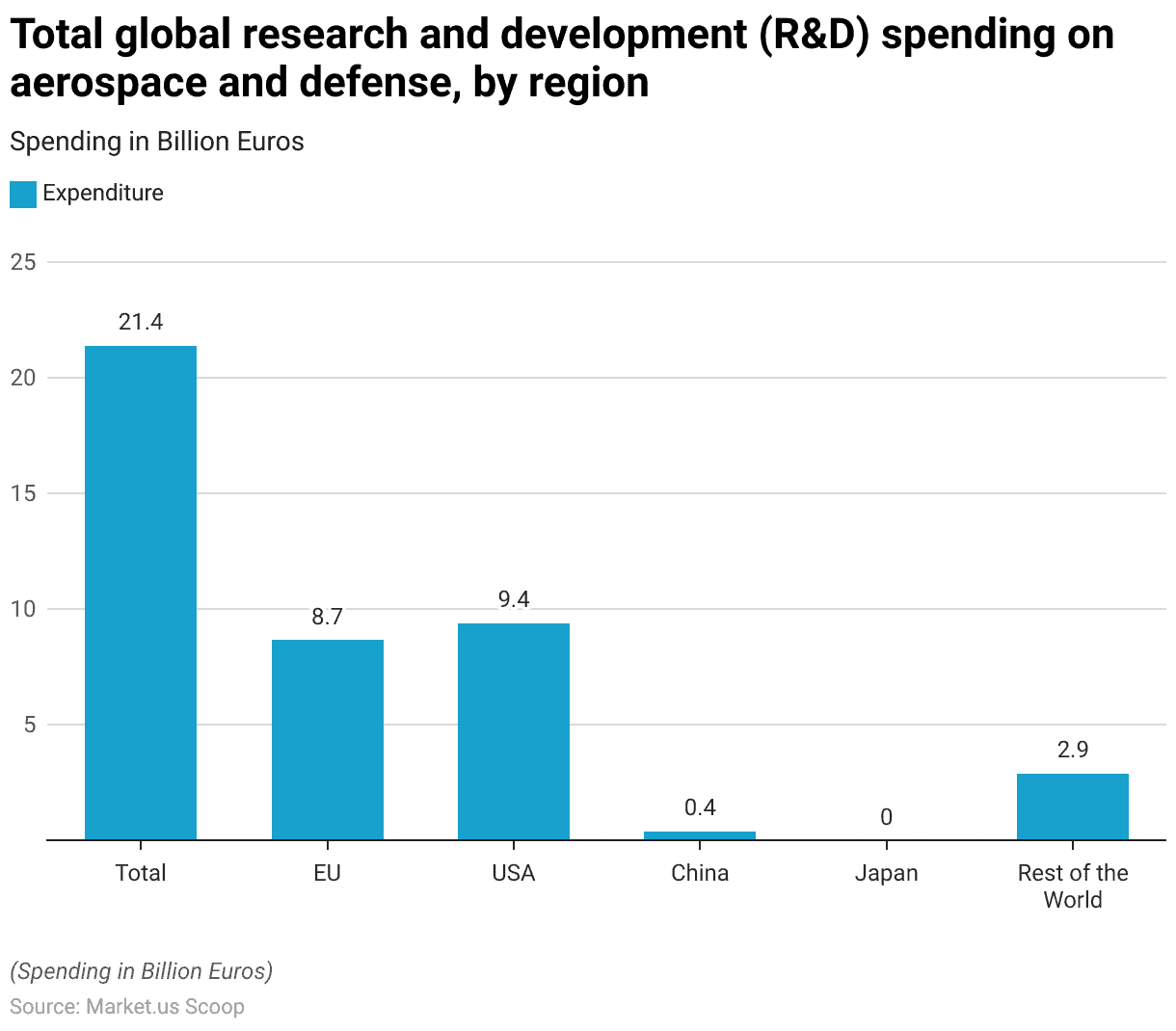
Regulations for Single-use Plastics in Aviation
- Various countries have introduced regulations to phase out or restrict single-use plastic products (SUPP) in the airline industry, with significant implications for airlines worldwide.
- In Australia, from 2021 to 2025, different states will phase out problematic SUPP, and airlines must comply with the National Packaging Targets. prohibiting the procurement of SUPP for use or sale in Australia.
- In Canada, starting December 2022, there is a prohibition on the manufacture, import, and sale of SUPP, including checkout bags, cutlery, and straws, with certain allowances for items onboard during turnarounds at Canadian airports but restricted in Canadian airspace.
- The European Union has banned the sale of SUPPs, such as plates and cutlery, since July 2021, with airlines required to comply with labeling rules for certain SUPPs like cups.
- In India, starting in July 2022, airlines and catering companies are prohibited from sourcing or using restricted SUPs.
- In China, restrictions were introduced in 2022 for airports handling over 2 million passengers and domestic flights. Extending to international flights in 2023, though enforcement details remain unclear.
- These global regulations necessitate significant adjustments in airline operations to meet sustainability goals and regulatory compliance.
(Source: International Air Transport Association (IATA))
Key Investments
- In 2022, global research and development (R&D) spending on aerospace and defense amounted to a total of 21.4 billion euros.
- The distribution of this spending varied significantly by region. The United States led with 9.4 billion euros, closely followed by the European Union, which contributed 8.7 billion euros.
- Meanwhile, the rest of the world combined for an expenditure of 2.9 billion euros.
- China’s investment was notably lower at only 0.4 billion euros, and Japan did not allocate any budget towards aerospace and defense R&D for that year.
- This data highlights the varying levels of investment and priorities different regions place on aerospace and defense research and development.
(Source: Statista)
Regulations for Aerospace Plastics
- Stringent global and national standards govern regulations for aerospace plastics to address both environmental concerns and safety requirements in the aerospace industry.
- The use of per- and polyfluorinated alkyl substances (PFAS), which are prevalent in aerospace plastics due to their durability and resistance to heat, is under significant scrutiny.
- The European Union, for instance, has proposed restrictions on PFAS that cover a wide array of applications, including aerospace. However, the unique needs of the industry have led to discussions about potential exceptions or tailored approaches for critical uses where alternatives may not offer the same performance or safety standards.
- Further, the United Nations has initiated efforts towards a legally binding global plastics treaty, aiming to address the lifecycle impacts of plastics, including those used in aerospace.
- This treaty is expected to influence future regulations on plastic use globally, shaping standards that could impact aerospace plastics by setting more stringent disposal, recycling, and production norms.
- In the United States, aerospace plastics are also subject to specific regulations under various environmental and safety directives. Regulatory frameworks continue to evolve as new environmental data and technologies emerge, influencing the development and application of aerospace plastics on a global scale.
- The complexity and specificity of these regulations require ongoing adaptation by aerospace manufacturers and suppliers to comply with both current and future environmental and safety mandates.
(Source: IAEG, CIEL, Nature)
Innovations and Developments in Aerospace Plastics Statistics
- In the aerospace industry, recent innovations in plastics are marked by a significant shift toward materials that are not only lightweight but also highly durable and adaptable to various applications.
- Key developments include the use of plastics like PEEK and DuPont™ Vespel® in engine parts, fuel systems, and interior applications such as seating and cabin dividers.
- These materials are chosen for their exceptional resistance to extreme temperatures, chemicals, and physical stresses, which is critical for safety and performance in aerospace environments.
- Companies like SABIC and Victrex are at the forefront of developing advanced plastic composites that are increasingly replacing metals in aerospace applications due to their advantageous weight-to-strength ratio.
- Moreover, these advancements are contributing to more sustainable practices within the industry. The shift towards plastics results in lighter aircraft, which inherently consume less fuel and produce fewer emissions, aligning with broader environmental goals.
- The innovation in aerospace plastics not only supports current industry needs but also sets the stage for future developments that could further transform aircraft design and functionality.
(Source: Thomasnet)
Recent Developments
Acquisitions and Mergers:
- Solvay acquires Cytec Industries: In 2023, Solvay, a global leader in advanced materials, completed the acquisition of Cytec Industries, a major supplier of aerospace-grade composites and plastics, for $5.5 billion. This merger enhances Solvay’s aerospace plastics portfolio, particularly for lightweight materials used in commercial aircraft manufacturing.
- Mitsubishi Chemical acquires Renegade Materials: In early 2024, Mitsubishi Chemical acquired Renegade Materials, a U.S.-based supplier of high-performance thermoset materials for aerospace applications, for $200 million. This acquisition aims to expand Mitsubishi’s presence in the aerospace plastics market, particularly in the space and defense sectors.
New Product Launches:
- Hexcel introduces HexPly® M901 thermoplastic resin: In 2023, Hexcel Corporation launched HexPly® M901, a next-generation thermoplastic resin designed for aerospace applications. This lightweight material is ideal for aircraft interiors and structures, offering 15% weight savings compared to traditional materials and reducing fuel consumption.
- Victrex launches PEEK polymer for aerospace: In mid-2023, Victrex introduced a new PEEK (Polyether ether ketone) polymer specifically designed for aerospace applications. The polymer provides enhanced strength and chemical resistance, improving safety and durability in high-temperature environments such as engines and fuselage components.
Funding:
- Toray Industries secures $300 million for aerospace plastics development: In 2023, Toray Industries, a Japanese chemical company specializing in composite materials, raised $300 million to enhance its R&D capabilities in aerospace plastics. The investment will be used to develop more sustainable, lightweight plastics for aircraft components.
- SABIC secures $150 million for aerospace thermoplastic expansion: In late 2023, SABIC, a global leader in specialty plastics, raised $150 million to expand its production capacity of aerospace-grade thermoplastics. This funding will support the development of advanced lightweight materials for both commercial and military aircraft.
Technological Advancements:
- 3D printing of aerospace plastics: By 2025, 30% of aerospace plastic components are expected to be produced using 3D printing technologies, allowing for more efficient and cost-effective manufacturing of complex parts.
- Development of sustainable aerospace plastics: With increasing pressure to reduce carbon emissions, aerospace manufacturers are shifting toward sustainable materials. By 2026, 20% of aerospace plastics are projected to be made from recycled or bio-based materials, significantly reducing environmental impact.
Conclusion
Aerospace Plastics Statistics – The aerospace industry has increasingly embraced plastics. Transitioning from traditional metals to advanced composites and high-performance polymers like PEEK and PEI.
These materials offer significant benefits, including reduced weight, improved fuel efficiency, enhanced corrosion resistance, and greater design flexibility.
This shift is driven by the need for materials that can withstand the harsh conditions of flight while meeting stringent safety standards.
With ongoing research and development, aerospace plastics are also becoming more recyclable and environmentally friendly, reflecting the industry’s commitment to sustainability.
As technology progresses, the role of plastics in aerospace is expected to grow. Highlighting their critical contribution to more efficient and sustainable aviation practices.
FAQs
Aerospace plastics are specialized high-performance polymers used in the construction of aircraft and spacecraft. They are chosen for their exceptional strength-to-weight ratio, corrosion resistance, and flexibility in design.
Plastics are used in aerospace for their lightweight properties, which contribute to fuel efficiency and overall performance enhancements. They also offer superior durability and resistance to environmental factors compared to many traditional materials.
Common types of aerospace plastics include Polyetheretherketone (PEEK), Polyetherimide (PEI), and Polymethylmethacrylate (PMMA), among others. Each type is selected based on specific properties like temperature resistance, strength, or optical clarity.
Aerospace plastics can be processed through various methods, including injection molding, compression molding, and CNC machining. The method chosen often depends on the complexity of the component and the type of plastic used.
The future of aerospace plastics looks promising with continuous advancements in polymer science and composite technology. Innovations are likely to produce even lighter and stronger materials that could further revolutionize aerospace engineering. Focusing particularly on sustainability and performance.
Discuss your needs with our analyst
Please share your requirements with more details so our analyst can check if they can solve your problem(s)
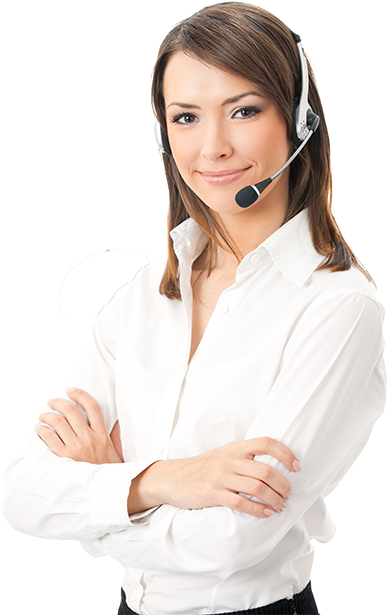