Table of Contents
Introduction
Aerospace 3D Printing Market is poised for substantial growth, projected to expand from USD 2.8 Billion in 2023 to approximately USD 15.9 Billion by 2033. This impressive growth trajectory represents a Compound Annual Growth Rate (CAGR) of 19.2% during the forecast period from 2024 to 2033. This robust expansion underscores the increasing adoption of 3D printing technologies in the aerospace sector, driven by the demand for lighter, more efficient aircraft components and the ongoing innovations in 3D printing materials and techniques.
Aerospace 3D printing, also known as additive manufacturing, involves creating three-dimensional objects from a digital file by layering materials. This technology has revolutionized the aerospace industry by allowing for the production of complex parts that are lighter and stronger than those made through traditional manufacturing methods. The capability to print components on-demand reduces waste, decreases the storage of inventory, and shortens the supply chain, which can lead to significant cost reductions.
The market for aerospace 3D printing is experiencing rapid growth, driven by the increasing adoption of this technology among aerospace manufacturers. This growth is fueled by the demand for newer aircraft designs with improved performance and fuel efficiency. Airlines are seeking these innovative solutions to reduce their operational costs and environmental impact, which in turn drives the expansion of 3D printing applications in aerospace.
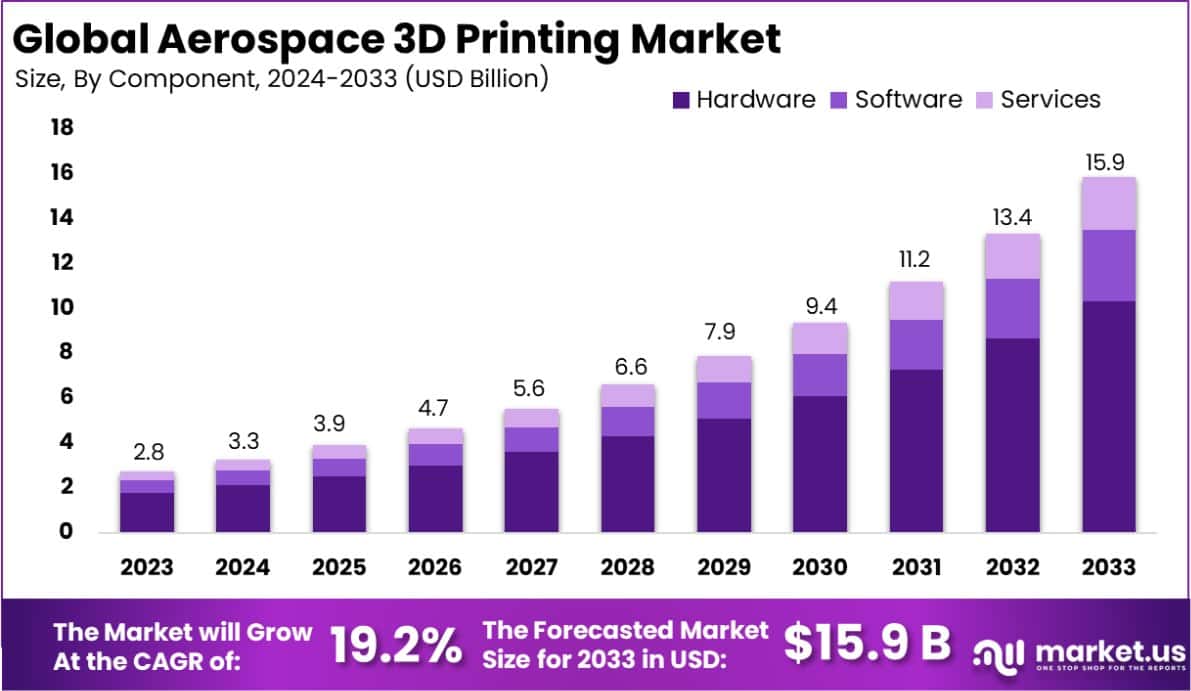
The growth of the aerospace 3D printing market can be attributed to several factors. Firstly, the need for more efficient and lightweight aircraft is escalating as companies aim to meet stringent environmental regulations and reduce fuel consumption. Secondly, the advancements in 3D printing technology, such as the development of new materials suitable for aerospace applications, enhance the appeal of this manufacturing method. Additionally, the aerospace industry’s demand for customized parts for prototyping and small batch production continues to grow, presenting significant opportunities for market expansion.
Key Takeaways
- The Global Aerospace 3D Printing Market is projected to escalate substantially from USD 2.8 Billion in 2023 to an estimated USD 15.9 Billion by 2033. This growth is anticipated at a Compound Annual Growth Rate (CAGR) of 19.2% during the forecast period spanning 2024 to 2033.
- In the component segmentation of the Aerospace 3D Printing Market in 2023, Hardware maintained a commanding lead, securing over 64.8% of the market share.
- The Selective Laser Melting (SLM) technology was predominant in the technology segment of the Aerospace 3D Printing Market in 2023, accounting for more than 47.5% of the market share.
- Prototyping applications dominated the application segment of the Aerospace 3D Printing Market in 2023, capturing more than 54.2% of the market share.
- In the materials segment, Metal was the leading material used in Aerospace 3D Printing in 2023, comprising over 58.7% of the market share.
- For the platform segmentation in 2023, Aircraft platforms held the largest market share in Aerospace 3D Printing, with more than 59.4% of the market.
- In the regional analysis, North America was the leading contributor to the Aerospace 3D Printing Market in 2023, holding a 41% market share and generating revenue of USD 1.12 Billion.
Aerospace 3D Printing Statistics
- The Global 3D Printing Market is projected to reach a value of USD 135.4 billion by 2033, a significant increase from USD 19.8 billion in 2023, representing a robust compound annual growth rate (CAGR) of 21.2% during the forecast period from 2024 to 2033.
- In recent industry surveys, 71% of businesses reported increased utilization of 3D printing technologies in 2022 compared to the previous year. Furthermore, analysts anticipate a 17% growth in the 3D printing market in 2023 alone, equating to an additional $19.9 billion in revenue generated through 3D printing activities.
- The industrial metal additive manufacturing market experienced a growth of over 20% in 2022, reaching a valuation of approximately $3.25 billion. The sector is forecasted to continue its rapid expansion with a projected CAGR of nearly 30% through 2027.
- Key players in the aerospace and defense (A&D) industry, such as Airbus and Raytheon Technologies, are actively leveraging 3D printing technologies. Raytheon, for example, is utilizing nearly 70 3D printers across its global operations to produce up to 2,500 face shield headbands per week.
- By 2025, the construction sector is anticipated to contribute nearly 55% to the overall 3D printing concrete market. Similarly, the jewelry industry is expected to account for around 15% of the 3D printing market share by 2027.
- In the aerospace industry, the market share of 3D printing is projected to exceed 20% of the global market by 2025, while the automotive industry already holds a 20% share of the global market.
- Currently, 40% of companies worldwide are incorporating 3D printing into their production processes. In the United States, 75% of surveyed manufacturers have adopted some form of 3D printing technology, with 31% of industrial manufacturers using it for producing finished goods or components. Additionally, 45% of small and medium-sized businesses (SMBs) in the U.S. are utilizing 3D printing technology.
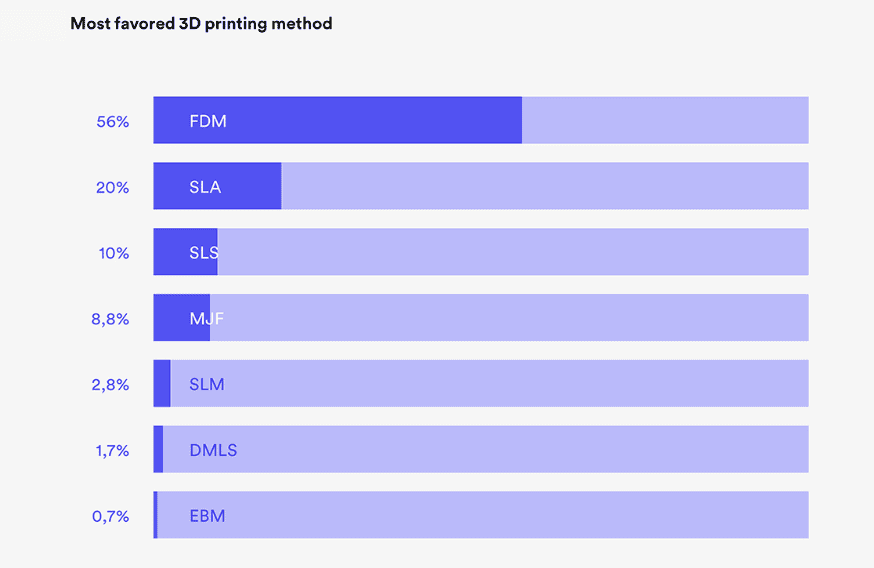
Source: protolabs.com
Emerging Trends
- Adoption of Advanced Materials: The aerospace 3D printing industry is seeing a significant shift towards the use of a wider variety of advanced materials. Innovations include engineering thermoplastics, composite polymer powders, and various metal powders, which are enhancing the capabilities of printed components in terms of durability, thermal resistance, and structural integrity.
- Expansion of Metal 3D Printing: Direct Metal Laser Sintering (DMLS) and other metal 3D printing technologies are increasingly adopted due to their ability to produce complex, lightweight, and strong aerospace components. This trend is expected to dominate the market due to the critical demand for performance optimization in aerospace applications.
- Integration of Software and Automation: Advances in software for generating G-code and automating the 3D printing process are pushing the boundaries of what can be manufactured, enabling non-planar and complex geometries that reduce material use and weight, crucial for aerospace components.
- Large-Scale and Rapid Production: The development of larger 3D printers and faster production techniques is being driven by the need for rapid prototyping and manufacturing of large aerospace components, reducing lead times and costs.
- Sustainability and Recycling: Increased focus on sustainability has led to the exploration of recycled materials for 3D printing and processes that minimize waste, addressing environmental concerns within the aerospace industry.
Top Use Cases in Aerospace 3D Printing
- Engine Components: 3D printing is extensively used to manufacture complex engine components that are lighter and more durable. Innovations such as 3D printed engine combustors are notable examples of how critical parts are being optimized for better performance and fuel efficiency.
- Prototyping and Tooling: Aerospace companies utilize 3D printing for rapid prototyping, allowing for faster iteration and testing of designs. This reduces development time and costs significantly, which is crucial in the highly competitive aerospace sector.
- Manufacturing of Structural Components: The ability to print large structural components for aircraft is one of the most impactful uses of 3D printing, offering enhanced customization and the reduction of assembly times and material waste.
- On-Demand Spare Parts: 3D printing enables the on-demand production of spare parts for maintenance and repair, significantly reducing the storage and logistics costs associated with maintaining large inventories of parts.
- Space Exploration Applications: The production of lightweight components for spacecraft, including parts that can be printed directly in space, is an emerging application of 3D printing. This use case is vital for reducing the costs and logistical challenges of space missions.
Major Challenges
- Material Limitations and Cost: Aerospace companies continue to face challenges with the range and cost of materials suitable for 3D printing. These materials must meet strict aerospace standards, which limits the availability of appropriate options and often comes at a high cost.
- Scalability and Production Rates: Scaling up 3D printing to meet the demands of large-scale production remains complex, with companies needing to carefully plan and optimize their workflows to achieve efficient and scalable production.
- Technology Adoption and Training: The integration of 3D printing in aerospace is hindered by cultural rigidity and a lack of trained personnel. The sector’s high safety standards require extensive training and adaptation, which can slow down the implementation of new technologies.
- Supply Chain Integration: Integrating 3D printing into existing supply chains is challenging. Disruptions in the supply of essential materials like resins and metals can lead to production delays and increased costs.
- Regulatory and Certification Processes: The aerospace industry is heavily regulated, and getting 3D printed parts certified can be a lengthy and expensive process. This is particularly challenging when introducing new materials or technologies.
Top Opportunities
- Cost Reduction and Efficiency: 3D printing allows for the production of parts with reduced need for expensive tooling, molds, and dies, which is especially beneficial for low-volume or highly specialized components. This process also minimizes material waste and can contribute to lower operational costs through the production of lighter parts.
- Enhanced Design and Performance: The technology enables the creation of complex part geometries that are difficult or impossible to achieve with traditional manufacturing methods. This can lead to improved performance characteristics of aerospace components, such as reduced weight and increased strength.
- Rapid Prototyping and Innovation: 3D printing significantly accelerates the development process, enabling quicker prototyping and testing. This rapid prototyping capability allows for faster iteration and innovation in the design of new aerospace components and systems.
- Customization and Flexibility: The ability to produce customized parts on demand provides significant flexibility in manufacturing and maintenance, allowing aerospace companies to produce parts as needed and reduce inventory costs.
- Sustainability and Environmental Benefits: 3D printing contributes to sustainability in manufacturing through the efficient use of materials and energy. The technology’s additive nature reduces waste and energy consumption compared to traditional subtractive manufacturing processes.
Recent Developments
3D Systems Corporation
New Product Launches: In late 2023, 3D Systems (NYSE: DDD) introduced a high-speed metal 3D printer designed specifically for aerospace applications. This machine is expected to enhance production efficiency for aerospace components, reducing costs and improving speed.
Norsk Titanium’s Partnerships and Innovations
In 2023, Norsk Titanium has continued to innovate in the aerospace sector by forming strategic partnerships and introducing new 3D printing technologies that focus on producing titanium components. These advancements aim to reduce manufacturing costs and time while increasing the adoption of 3D printing in the aerospace industry.
GE Additive
Technological Advancements: GE Additive launched an updated version of its Binder Jet technology in early 2024. This new technology allows for the production of larger and more complex metal parts, which are increasingly demanded by the aerospace sector. The new system is expected to improve production precision and efficiency.
Ultimaker’s Product Launch
In 2023, Ultimaker BV launched a new series of 3D printers designed for industrial applications, including aerospace, in 2023. These printers are equipped with advanced features that enhance precision and reliability, catering to the increasing demand for 3D-printed parts in the aerospace industry
Conclusion
In conclusion, the aerospace 3D printing market is poised for substantial growth, driven by the industry’s demand for cost-effective, lightweight, and strong components that comply with new environmental standards. As technology advances and adoption increases, aerospace companies are likely to continue integrating 3D printing into their manufacturing processes. This integration represents a promising opportunity for the industry to innovate and evolve, ensuring more efficient operations and sustainable practices in the future.
You May Also Like To Read
- “3D Printing Market: Transforming Design and Production Across Industries”
- “AI in 3D Printing Market: Transforming Manufacturing Processes with Smart Technology”
- “Aerospace AI Market: Revolutionizing Aviation with Intelligent Systems”
- “Food 3D Printing Market: Transforming the Future of Food Production”
Discuss your needs with our analyst
Please share your requirements with more details so our analyst can check if they can solve your problem(s)
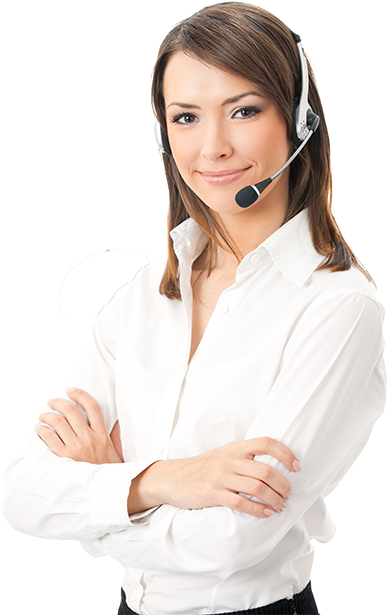