Table of Contents
- Introduction
- Editor’s Choice
- History and Evolution of Gas Detection Equipment
- Gas Detection Equipment Market Statistics
- Different Sensors Used in Gas Detection Equipment Statistics
- Comparison of Different Gas Sensor Types
- Ultrasonic Gas Leak Detectors
- Combustible Gas Detectors
- Relative Sensitivity vs. calibration Constants for Gases and Vapors
- Measurement Ranges for Electrochemical Dräger Sensors
- Gas Alarm Setpoints
- Key Spending and Investments
- Innovations and Developments in Gas Detection Equipment Statistics
- Regulations and Statistics for Gas Detection Equipment
- Recent Developments
- Conclusion
- FAQs
Introduction
Gas Detection Equipment Statistics: Gas detection equipment is essential for monitoring hazardous gases in environments such as industrial sites and confined spaces, ensuring worker safety.
These systems typically consist of sensors (like electrochemical or infrared) that detect gas levels, alarms to warn of dangerous concentrations, and controllers that display data and trigger warnings.
Gas detectors come in portable forms for individual use, as well as fixed systems for continuous monitoring of larger areas.
Regular calibration is needed to maintain accuracy, making these devices crucial for preventing accidents and protecting health in high-risk settings.

Editor’s Choice
- The Global Gas Detection Equipment Market size is expected to reach USD 10.2 billion by 2033.
- In 2021, the Global Gas Detection Equipment Market featured a diverse range of key players, with Airtest Technologies, Inc. leading the market, holding an 18% share.
- In 2021, the Global Gas Detection Equipment Market saw varying market shares across regions, with the Asia-Pacific (APAC) region leading at 32.6%.
- Infrared sensors can detect CO2 levels from 0-5,000 ppm, 0-5% volume, and even up to 0-100% volume, catering to a wide range of industrial, environmental, and safety monitoring needs.
- By 2025, significant investments in advanced methane monitoring technologies are expected, with North America leading the way. The region plans to invest $182 million each for satellites and aircraft, $52 million for drones, and $117 million for sensors.
- Companies like Dräger have introduced products like the Draeger X-am 2800, a mobile gas detector that provides real-time chemical exposure data and is equipped with robust connectivity features such as Bluetooth for cloud integration.
- In the United States, recent updates include the EPA’s implementation of new performance standards aimed at reducing methane and volatile organic compound emissions from the oil and gas sector, utilizing advanced technologies like Gas Mapping LiDAR for regulatory compliance.
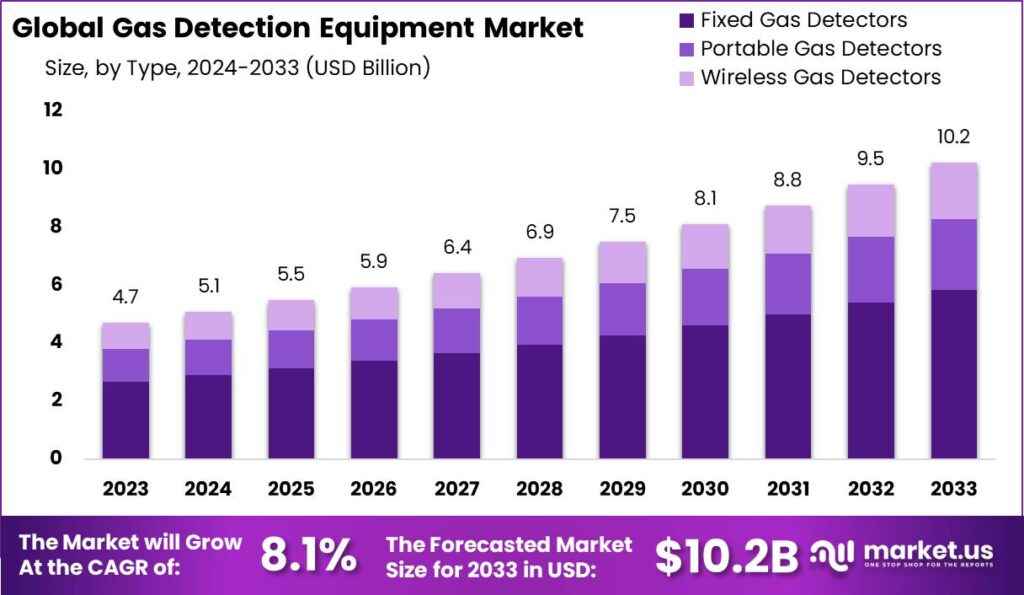
History and Evolution of Gas Detection Equipment
- The history and evolution of gas detection equipment span several centuries, reflecting significant advancements in safety technology.
- Initially, rudimentary methods such as canaries in coal mines and simple flame devices like the Davy lamp in 1815 marked the early attempts to detect dangerous gases.
- By the 18th century, advances in chemistry, led by figures like Carl Wilhelm Scheele, provided a more scientific approach to detecting gases like sulfur dioxide and ammonia.
- The transition to electrical technologies began in the late 19th century, culminating in the development of the Nernst lamp, an early type of electrical gas detector.
- In the 1920s, further advancements were seen with the invention of the catalytic combustion sensor by Dr. Oliver Johnson, which greatly improved the detection of combustible gases in industrial settings.
- Throughout the 20th century, the field continued to evolve with the introduction of technologies that utilized electronic sensors for more accurate and rapid gas detection, making extensive use of developments in material science and electronic engineering.
- By the 1980s, the shift towards miniaturized electronic detectors revolutionized the industry, making devices more portable and affordable, thus expanding their use across various industries beyond mining, such as in-home safety and industrial applications.
- Today, gas detection equipment incorporates sophisticated technologies, including infrared, electrochemical sensors, and even wireless networks for real-time monitoring, reflecting ongoing innovation and adaptation to new safety challenges in diverse environments.
- This progression from simple mechanical tools to complex electronic systems illustrates the dynamic nature of the gas detection field, continually enhancing safety measures in response to the ever-present risks posed by toxic and flammable gases.
(Sources: DOD Technologies, Interscan Gas Detectors, Atex, Industrial Automation, GazDetect)
Gas Detection Equipment Market Statistics
Global Gas Detection Equipment Market Size Statistics
- The Global Gas Detection Equipment Market has been steadily growing, with its valuation increasing year-on-year from 2023 to 2033 at a CAGR of 8.1%.
- In 2023, the market size was estimated at USD 4.7 billion.
- This upward trajectory continues as the market is projected to reach USD 5.1 billion in 2024 and further expand to USD 5.5 billion in 2025.
- By 2026, the market is expected to grow to USD 5.9 billion, reflecting increasing adoption and advancements in gas detection technologies.
- The market size will continue to rise, reaching USD 6.4 billion in 2027 and USD 6.9 billion in 2028.
- This growth pattern remains robust, with the market expected to surpass USD 7.5 billion by 2029, driven by heightened safety regulations and industrial advancements.
- By 2030, the market size is forecasted to reach USD 8.1 billion, followed by USD 8.8 billion in 2031.
- The growth accelerates further in subsequent years, with the market expected to hit USD 9.5 billion in 2032 and finally reach USD 10.2 billion by 2033.
- The consistent increase in market valuation reflects the growing demand for gas detection solutions across various sectors, including industrial safety, environmental monitoring, and healthcare, as organizations prioritize enhanced safety measures and compliance with stringent regulations.
(Source: market.us)
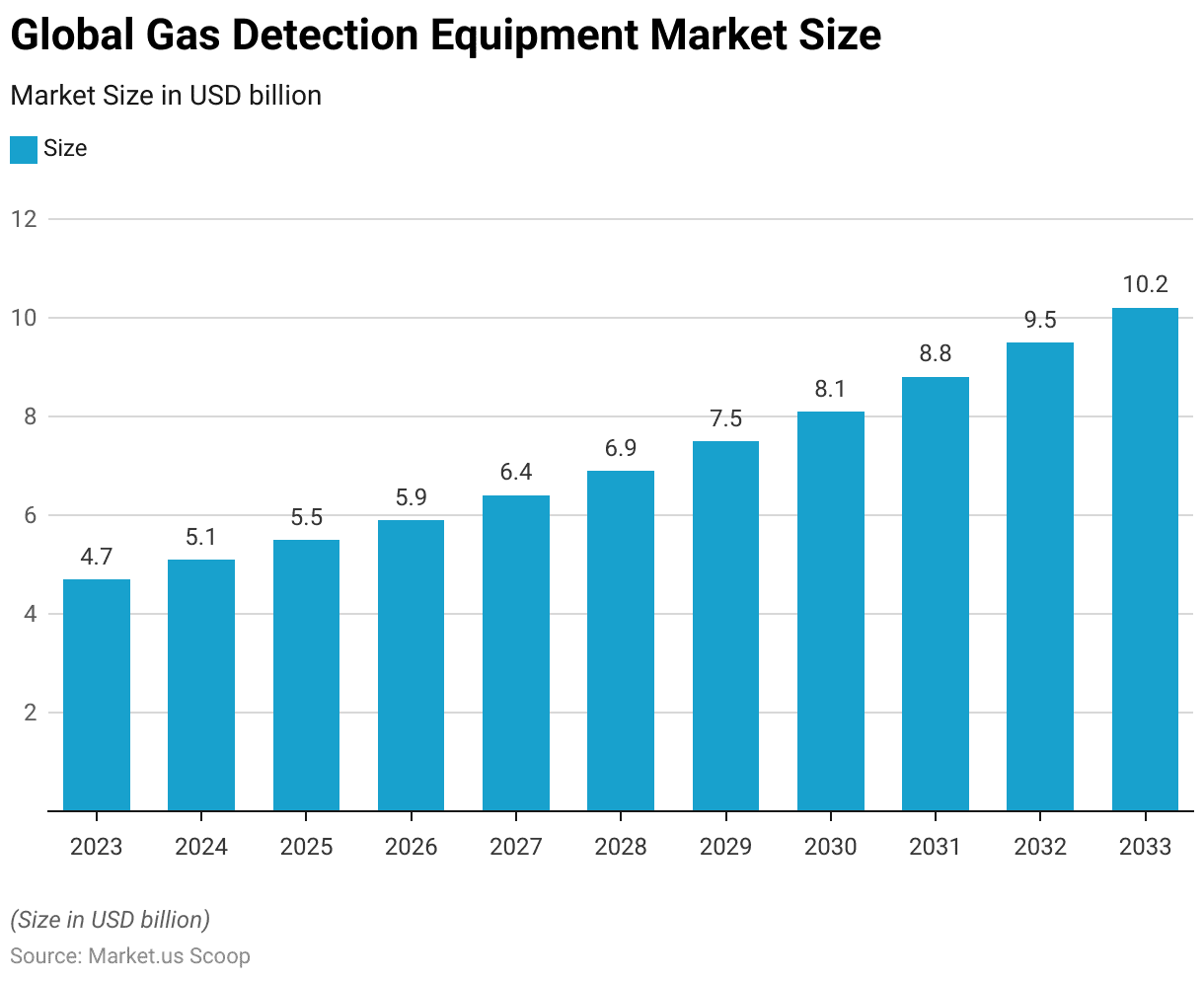
Competitive Landscape of Global Gas Detection Equipment Market Statistics
- The competitive landscape of the Global Gas Detection Equipment Market in 2021 showcased a diverse range of prominent players contributing to the market’s dynamics.
- Airtest Technologies, Inc. led the market with the highest share, capturing 18% of the total market.
- Close behind was ABB, holding a significant 17% share, reflecting its robust presence in gas detection solutions.
- FLIR Systems, Inc. accounted for 9% of the market share, emphasizing its focus on thermal imaging and gas detection technologies.
- Fluke Corporation, General Electric Company, Opgal, and Thermo Fisher Scientific, Inc. each secured 8% of the market, highlighting their strong foothold in providing advanced gas detection equipment for various industrial applications.
- Siemens followed with a 7% market share, showcasing its innovative approach to safety technologies and monitoring systems.
- Additionally, other key players collectively held 16% of the market, indicating a competitive environment with numerous smaller yet significant contributors.
- These companies play an essential role in addressing niche requirements and enhancing the technological capabilities of the gas detection equipment sector.
- This distribution of market shares illustrates healthy competition among leading companies, driven by continuous innovation, stringent safety regulations, and the increasing need for gas detection systems across industries.
(Source: market.us)
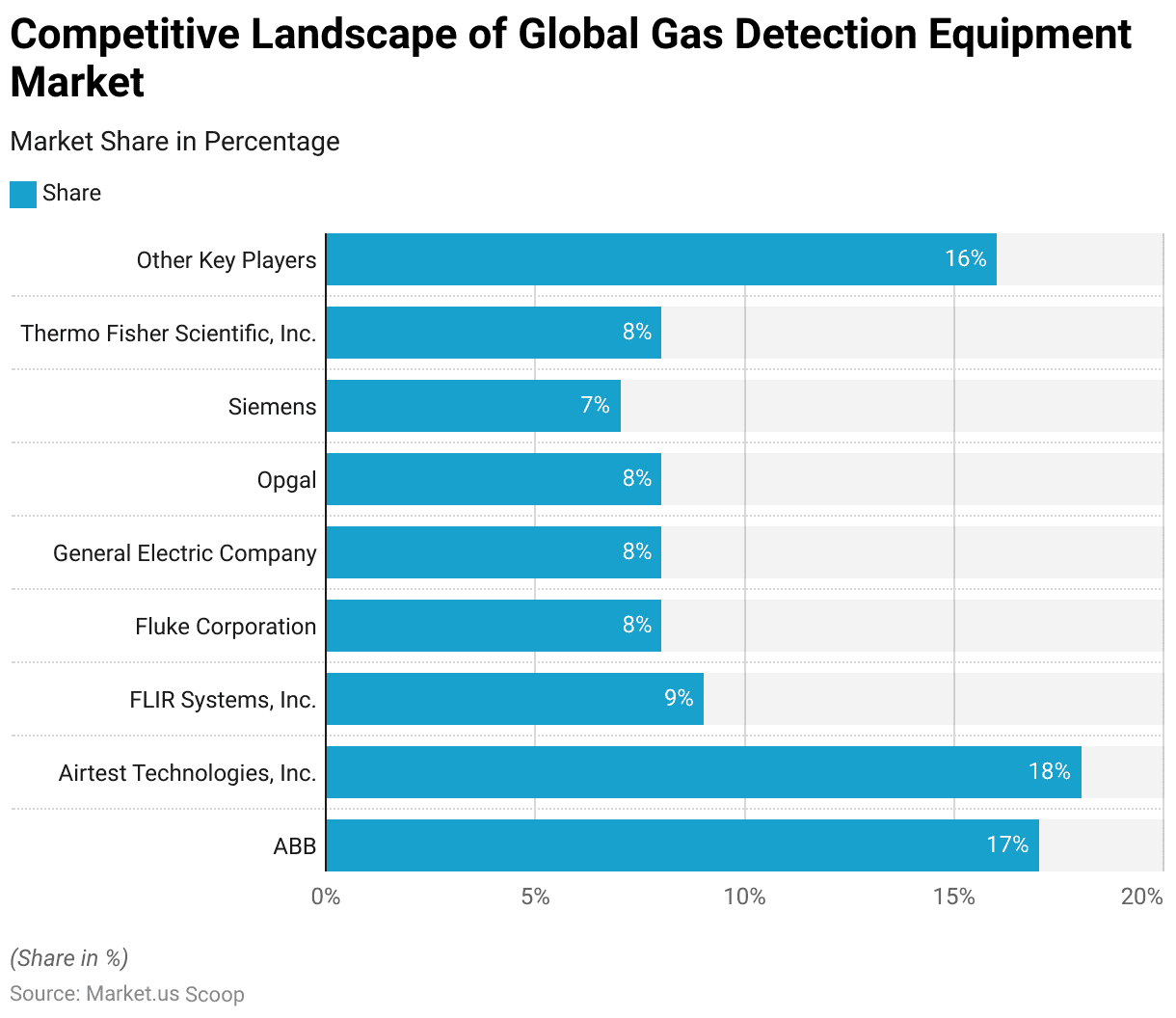
Global Gas Detection Equipment Market Share – By Region Statistics
- The regional distribution of the Global Gas Detection Equipment Market in 2021 highlighted significant variations in market share across key geographical regions.
- The Asia-Pacific (APAC) region emerged as the largest contributor, accounting for 32.6% of the total market share.
- This dominance can be attributed to rapid industrialization, the expansion of manufacturing sectors, and stringent safety regulations in countries such as China, India, and Japan. The growing adoption of advanced safety equipment in these nations has further bolstered the region’s market position.
- North America held the second-largest market share at 28.0%, driven by the presence of established players, technological advancements, and strict workplace safety standards, particularly in the United States and Canada.
- The region’s focus on ensuring compliance with regulatory norms for hazardous gas monitoring continues to fuel the demand for gas detection equipment.
- Europe accounted for 20.0% of the market share, reflecting the region’s emphasis on environmental sustainability and industrial safety.
- The stringent regulatory framework in the European Union, coupled with the widespread adoption of advanced monitoring systems in industries such as oil & gas and chemicals, has contributed to its substantial market presence.
- South America represented 11.0% of the market share, driven by increasing industrial activities and investments in the oil & gas and mining sectors.
- The Middle East and Africa (MEA) held an 8.4% share, supported by the growing demand for gas detection systems in oil-rich economies and the expanding construction sector.
- These regional dynamics underline the diverse growth opportunities in the global gas detection equipment market, shaped by unique industry demands and regulatory environments.
(Source: market.us)
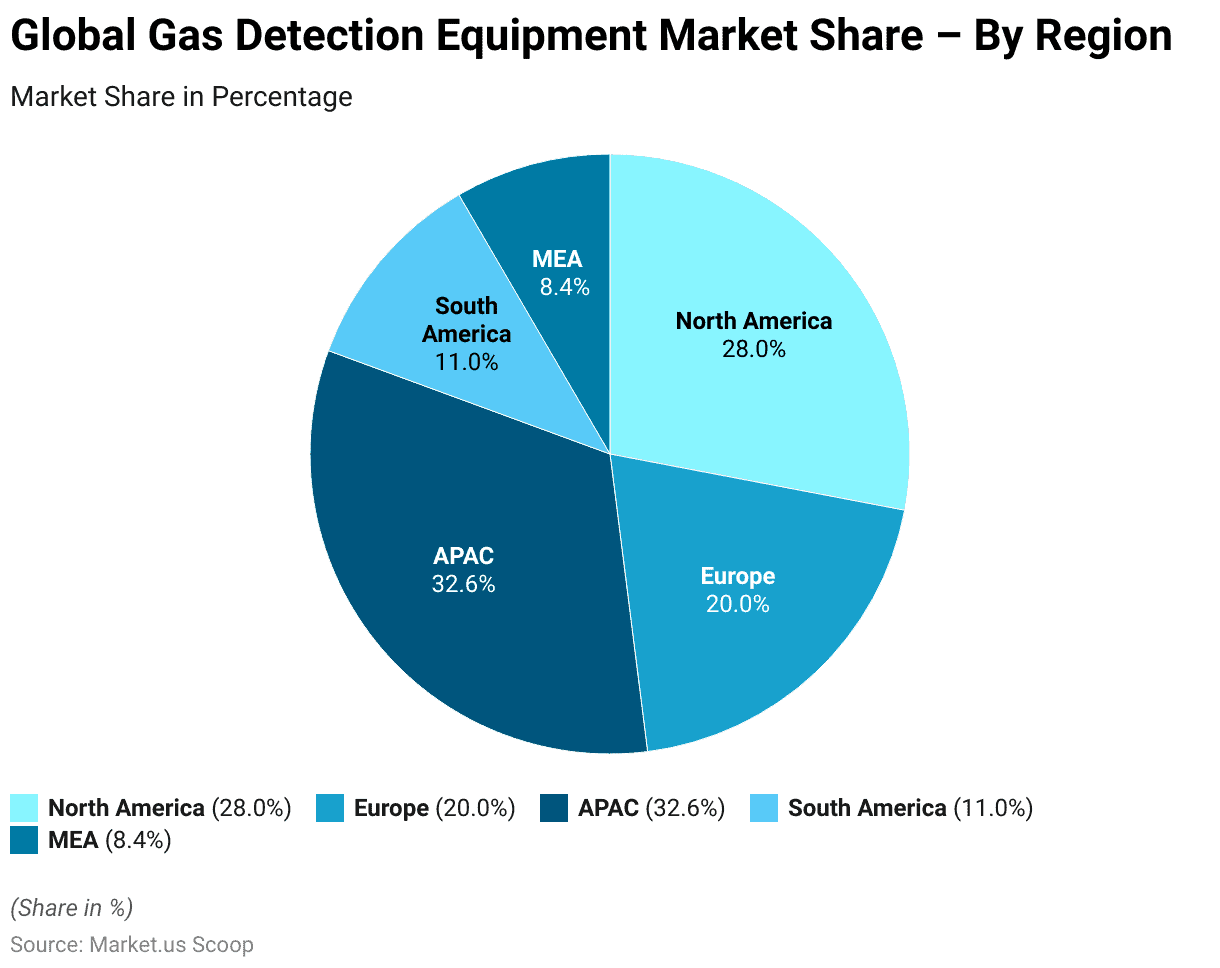
Different Sensors Used in Gas Detection Equipment Statistics
Electrochemical Sensors
- Electrochemical sensors, widely used for gas detection, have varying ranges, life expectancies, shelf lives, and calibration frequencies based on the gas they monitor.
- For instance, ammonia (NH3) sensors with a range of 0-500 ppm have a life expectancy of 2 years and require calibration every 6 months. Carbon monoxide (CO) sensors are available in two series: the 4 Series (0-200 ppm) with a 3-year life expectancy and the 7 Series (0-200 ppm) with a 5-year lifespan.
- Chlorine (Cl2) sensors also come in two variants: the 4 Series (0-5 ppm), lasting 3 years, and the 7 Series (0-5 ppm), with a life expectancy of 5 years.
- Similarly, chlorine dioxide (ClO2) sensors (0-1 ppm), ethylene (C2H4) sensors (0-200 ppm), ethylene oxide (C2H4O) sensors (0-20 ppm), fluorine (F2) sensors (0-1 ppm), and hydrogen (H2) sensors (0-2000 ppm) all have a life expectancy of 2 years and require calibration every 6 months, particularly in applications where people routinely work.
- Hydrogen sulfide (H2S) sensors are available in the 4 Series (0-50 ppm) with a 2-year life expectancy and the 7 Series (0-50 ppm) with a lifespan exceeding 5 years. Other notable sensors include hydrogen chloride (HCl), hydrogen cyanide (HCN), nitric oxide (NO), ozone (O3), phosphine (PH3), silane (SiH4), and sulfur dioxide (SO2), all with a 2-year life expectancy.
- Nitrogen dioxide (NO2) sensors are available in the 4 Series (0-10 ppm) with a 3-year lifespan and the 7 Series (0-10 ppm) with a 5-year life expectancy. Oxygen (O2) sensors, designed to detect 0-25% volume, have a life expectancy of 3 years.
- All sensors have a shelf life of less than 12 months and should be calibrated every 6 months for optimal performance, especially in environments where safety is critical.
(Source: Critical Environment Technologies)
Catalytic Sensors
- Catalytic sensors are widely utilized for detecting combustible gases, with specific applications for hydrogen (H2), methane (CH4), and propane (C3H8).
- These sensors are designed to operate effectively within a range of 0-100% of the lower explosive limit (LEL) for each gas.
- They have a robust life expectancy of 5 years, making them reliable for long-term use in industrial and safety-critical environments.
- Unlike other sensor types, catalytic sensors do not have a specified shelf life and typically do not require regular calibration, simplifying their maintenance.
- These features make them ideal for continuous monitoring in various applications where detecting combustible gas levels is essential for safety and regulatory compliance.
(Source: Critical Environment Technologies)
Solid State Refrigerant Sensors
- Solid-state refrigerant sensors are specifically designed to detect a variety of refrigerant gases, including R22, R134A, R402A, R404A, R407C, R410A, R422D, and R507A, within a range of 0-2,000 ppm.
- These sensors also monitor total volatile organic compounds (TVOCs) in a range of 0-500 ppm.
- Both sensor types offer a robust life expectancy of 5 years, ensuring long-term reliability in refrigeration and air quality monitoring applications.
- Notably, these sensors do not have a specified shelf life, adding to their versatility in storage and deployment.
- For optimal performance and accuracy, solid-state refrigerant sensors require calibration every 12 months, especially in environments where precise monitoring of refrigerants and VOCs is critical for maintaining safety and efficiency.
(Source: Critical Environment Technologies)
Non-Dispersive Infrared (NDIR) Refrigerant Sensors
- Non-dispersive infrared (NDIR) refrigerant sensors are highly specialized for detecting a wide range of refrigerants, including R22, R134A, R404A, R407A, R407C, R407F, R410A, R422A, R422D, R427A, R507A, HFO1234YF, and HFO1234ZE, within a range of 0-2,000 ppm.
- Additionally, these sensors are capable of monitoring R123 and SF6 gases in a range of 0-1,000 ppm.
- Both categories of NDIR sensors offer a robust life expectancy of 5 years, making them suitable for long-term applications in refrigeration and gas monitoring.
- These sensors do not have a specified shelf life, ensuring flexibility in storage and deployment.
- For optimal accuracy and reliability, the sensors require calibration every 2 years, particularly for applications involving precise monitoring of refrigerants and gases to ensure safety and compliance with environmental standards.
(Source: Critical Environment Technologies)
Infrared Sensors
- Infrared sensors designed for carbon dioxide (CO2) detection are highly reliable and versatile, with applications across various concentration ranges.
- These sensors can detect CO2 levels from 0-5,000 ppm, 0-5% volume, and even up to 0-100% volume, catering to a wide range of industrial, environmental, and safety monitoring needs.
- With a robust life expectancy of 8 years, these sensors are built for long-term operation, ensuring consistent performance over extended periods.
- Additionally, they do not have a specified shelf life, making them flexible for storage and immediate deployment when needed.
- This combination of durability, accuracy, and adaptability makes infrared CO2 sensors an essential tool for monitoring and managing CO2 concentrations in diverse environments.
(Source: Critical Environment Technologies)
Photo Ionization Detector (PID) Sensors
- Photoionization Detector (PID) sensors are designed for the detection of Total Volatile Organic Compounds (TVOCs) across two primary ranges: 0-30 ppm and 0-300 ppm.
- These sensors are widely used for monitoring air quality and ensuring safety in environments where VOC levels can pose risks to health or safety.
- While specific details on life expectancy and shelf life are not provided, their calibration frequency and operational reliability depend on the specific application and environmental conditions.
- These sensors are integral to applications requiring precise and sensitive detection of VOCs in various industrial and environmental settings.
(Source: Critical Environment Technologies)
Comparison of Different Gas Sensor Types
- Sensor response times and accuracies vary depending on the type of sensor used, as tested by IGD under standard conditions.
- Pellistor sensors exhibit a response time (T90) of less than 10 seconds with an accuracy of ±2% LEL, while infrared sensors respond within 15 seconds with an accuracy of ±2% of their range.
- Electrochemical sensors show varying response times based on the gas detected: sensors for CO, H2S, and SO2 have a response time of less than 30 seconds, while those for O2 and NO2, Cl, and NH3 respond within 15 and 50 seconds, respectively, all with an accuracy of ±2% of range.
- The comparison between the T750X and T750XD models reveals several shared features, including compatibility with Pellistor, infrared, PID, toxic, and O2 sensors. Both models offer two mA inputs, two digital inputs, and 2 SSR outputs.
- They feature a relay option, with the T750XD adding support for a 2x RGB LCD.
- Non-intrusive calibration is supported in both models. Additionally, both models are compatible with control panels such as T650, T635, and T750, accommodating up to 32 detectors per cable run.
- These specifications highlight the versatility and efficiency of the T750 series in gas detection applications.
(Source: International Gas Detectors)
Ultrasonic Gas Leak Detectors
- Ultrasonic gas leak detectors work by “listening” to the sound created by gas escaping from a leak instead of measuring the concentration of gas in the air.
- These detectors pick up the acoustic noise generated by gas leaks in open, well-ventilated spaces to identify if a leak is present.
- Unlike traditional detectors, ultrasonic devices are not affected by factors like wind direction, gas dilution, or the direction of the leak.
- The detection range of these devices typically covers a radius of 4 to 20 meters (13–65 feet) around the detector, depending on the noise levels in the area.
- For example, in high-noise environments like near gas compressors, the detection radius may be 6–8 meters (20–26 feet) for gas leaks with a rate of 0.1 kg/s.
- In quieter areas, the same detector can cover a radius of 10–12 meters (33–39 feet) for the same leak rate.
- To avoid false alarms, the detectors are programmed to filter out normal background noise by performing a baseline noise survey during setup.
- These sensors are highly responsive and capable of identifying leaks in less than one second, making them an efficient and reliable solution for gas leak detection in various industrial settings.
(Source: Science Direct)
Combustible Gas Detectors
- Combustible gas detectors are commonly placed in buildings and at the air intakes of HVAC systems.
- They are also installed in outdoor areas where hydrocarbon vapors might be present, such as truck unloading stations that are often unmanned.
- These detectors are especially important in living quarters, high-value computer rooms, and offices that store critical records, ensuring safety in these key areas.
- Typically, these detectors have two alarm levels: 20% and 60% of the lower flammable limit (LFL).
- In locations with multiple detectors, a voting system can be used to determine the appropriate response.
- For example, if one 20% alarm is triggered, all hot work must stop, but other tasks can continue.
- However, if three 20% alarms or one 60% alarm is triggered, it signals the need for an emergency response.
- There are also specialized detectors designed to sense specific gases such as hydrogen, carbon monoxide, and hydrogen sulfide, providing advanced protection against dangerous leaks in sensitive areas.
(Source: Science Direct)
Relative Sensitivity vs. calibration Constants for Gases and Vapors
- The correction factors and calibration constants for various gases and vapors provide a clear understanding of their relative sensitivity and required calibration adjustments in terms of the Lower Explosive Limit (LEL).
- Methane, used as the reference gas, has a relative sensitivity of 1.00 and a calibration constant of 20.
- Propane and n-butane exhibit relative sensitivities of 0.63 and 0.59, respectively, with both requiring a calibration constant of 35.
- Similarly, n-Pentane has a sensitivity of 0.53 and a calibration constant of 40.
- Heavier hydrocarbons like n-hexane, N-Heptane, and n-octane show lower sensitivities of 0.42, 0.42, and 0.39, requiring calibration constants of 50, 50, and 55, respectively.
- Hydrogen and Methanol have sensitivities of 0.69 and 0.70 with calibration constants of 30.
- Ethanol and Iso Propyl Alcohol have lower sensitivities of 0.48 and 0.38, needing constants of 40 and 55, respectively.
- Acetone and Methyl Ethyl Ketone share the same sensitivity of 0.41 and calibration constant of 50.
- Benzene and Toluene exhibit sensitivities of 0.39 and 0.34 with calibration constants of 55 and 60.
- Di-ethyl Ether and Cyclohexane have sensitivities of 0.52 and 0.43, requiring calibration constants of 10 and 50, respectively.
- Ammonia, with the highest sensitivity of 1.24, requires a calibration constant of 15.
- These values highlight the variation in detector sensitivity and calibration requirements across different gases and vapors.
(Source: International Gas Detectors)
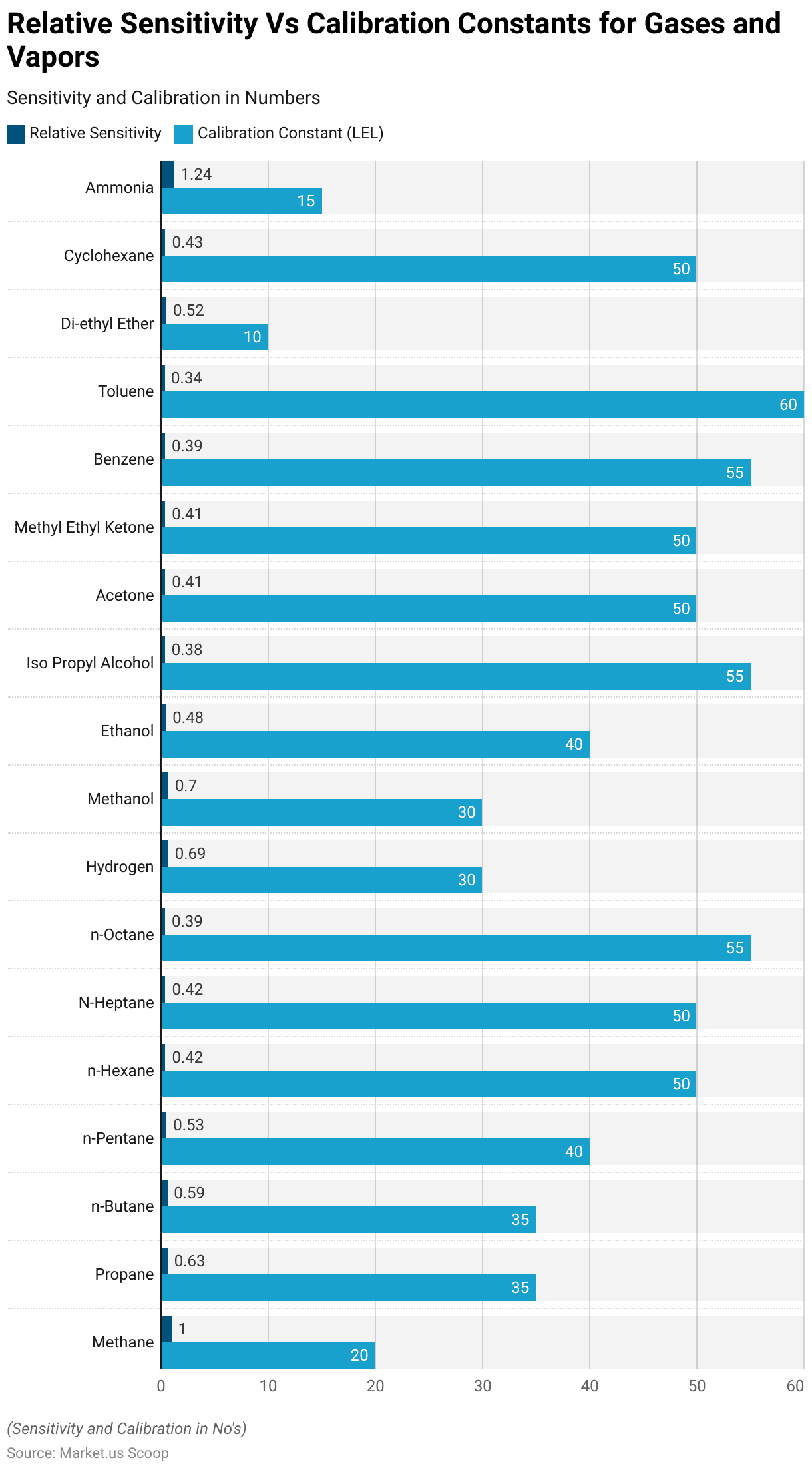
Measurement Ranges for Electrochemical Dräger Sensors
- Electrochemical Dräger sensors are designed to detect a wide range of gases with adjustable measurement ranges.
- For acidic compounds, the measurement range spans from 3 ppm to 30 ppm.
- Ammonia can be detected in ranges of 50–300 ppm and 200–1000 ppm, while carbon monoxide ranges from 50–200 ppm to 1000–5000 ppm.
- Chlorine can be measured from 1 ppm to 50 ppm, and hydrazine from 0.3 ppm to 3 ppm.
- Hydrides are detectable in ranges of 0.3 ppm to 1–20 ppm, while hydrogen ranges from 500 ppm to 3000 ppm.
- Hydrogen chloride is measurable from 20 ppm to 100 ppm, and hydrogen cyanide ranges from 10 ppm to 50 ppm.
- Hydrogen peroxide ranges from 1–1000 ppm to 50–7000 ppm, and hydrogen sulfide ranges from 10–100 ppm to 100–1000 ppm.
- Nitrogen dioxide has a range of 5 ppm to 100 ppm, and nitrogen monoxide spans 30 ppm to 200–500 ppm.
- Organic vapors are detectable in ranges of 20 ppm to 100–200 ppm, and ozone ranges from 0.5 ppm to 5 ppm.
- Oxygen is measurable from 5 Vol% to 25–100 Vol%, while phosgene ranges from 0.1 ppm to 1 ppm, and sulfur dioxide spans from five ppm to 100 ppm.
- These adjustable measurement ranges, as seen in devices like the Polytron 7000, ensure precise detection for diverse applications in industrial and environmental monitoring.
(Source: Dräger)
Gas Alarm Setpoints
- The suggested gas alarm setpoints provided by CET outline essential details for mounting, coverage, standard ranges, and alarm thresholds for various gases.
- Electrochemical (EC) sensors are typically installed in specific locations based on the properties of the gases they detect.
- For example, ammonia sensors are mounted on or near the ceiling, covering up to 3,000 ft² with alarm levels set at 25 ppm (low), 35 ppm (mid), and 250 ppm (high) within a 0-500 ppm range.
- Carbon dioxide (CO2) sensors, using infrared (IR) technology, are installed in the breathing zone with ranges of 0-2,000 ppm and 0-5% volume, with corresponding low, mid, and high alarms.
- Chlorine and other heavier gases like hydrogen chloride, hydrogen cyanide, and ozone require placement closer to the floor.
- For example, chlorine sensors operate in a range of 0-5 ppm with alarms set at 0.5 ppm (low), 0.7 ppm (mid), and 1.0 ppm (high).
- Similarly, combustible gases such as propane, methane, and hydrogen are monitored using catalytic (C) sensors, with alarm thresholds based on lower explosive limits (LEL), typically ranging from 10% (low) to 20% (high).
- Specialized sensors for freon refrigerants and TVOCs use metal oxide semiconductor (MOS) or IR technology.
- These sensors are placed near the floor and operate within ranges of 0-2,000 ppm or 0-3,500 ppm, with alarms starting at 250 ppm (low) and reaching 1,000 ppm (high).
- The mounting height, coverage, and specific ranges ensure optimal performance in various environments, providing robust safety measures for industrial and commercial spaces.
(Source: Critical Environment Technologies)
Key Spending and Investments
- By 2025, significant investments are expected across different regions for advanced methane monitoring technologies in the oil and gas industry, utilizing satellites, aircraft, drones, and sensors.
- North America leads the spending forecast with the highest investments across all categories, allocating $182 million each for satellite and aircraft monitoring, $52 million for drones, and $117 million for sensors. This reflects the region’s commitment to leveraging advanced technologies to mitigate methane emissions.
- Europe follows as the second-largest spender, dedicating $48 million to satellites, $37 million to aircraft, $34 million to drones, and $37 million to sensors. These figures highlight Europe’s focus on combining multiple technologies for comprehensive methane monitoring in line with its stringent environmental policies.
- Asia is projected to spend $25 million on satellites, $19 million on aircraft, $16 million on drones, and $21 million on sensors. While the investments are relatively smaller compared to North America and Europe, they reflect the region’s growing interest in enhancing methane monitoring capabilities.
- Latin America plans to invest $23 million in satellites, $9 million in aircraft, $20 million in drones, and $42 million in sensors. The emphasis on sensors in this region underscores its targeted approach to on-ground methane detection.
- The Middle East and Africa are forecasted to allocate $24 million to satellites, $9 million to aircraft, $7 million to drones, and $13 million to sensors.
- These investments, although modest compared to other regions, represent an important step towards improving methane emission monitoring in oil and gas operations within the region. This regional breakdown underscores a global effort to adopt advanced technologies to monitor and reduce methane emissions effectively.
(Source: Statista)
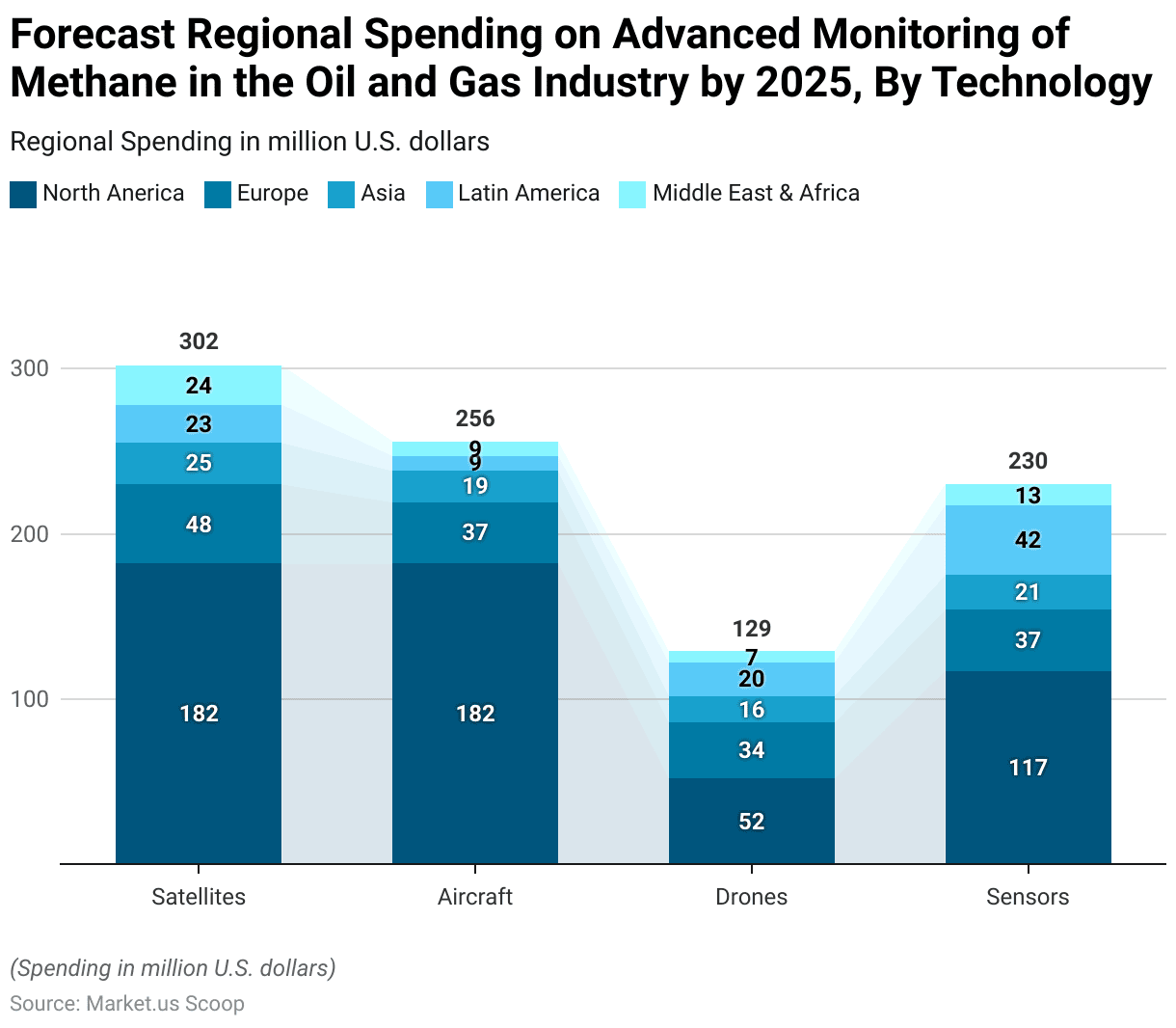
Innovations and Developments in Gas Detection Equipment Statistics
- The gas detection equipment market is experiencing rapid innovation and expansion, driven by advancements in technology and increasing safety requirements across industries.
- Key innovations include the integration of the Internet of Things (IoT) and artificial intelligence (AI) technologies, which enhance the real-time monitoring capabilities of gas detection systems.
- These technologies enable devices to provide instant alerts and detailed safety data, significantly improving response times and accuracy in hazardous environments.
- For example, CO2Meter‘s development of IoT-enabled smart gas detectors marks a significant advancement, allowing for remote data access and enhanced analytics, setting new standards for operational efficiency and safety.
- Additionally, companies like Dräger have introduced products like the Draeger X-am 2800, a mobile gas detector that provides real-time chemical exposure data and is equipped with robust connectivity features such as Bluetooth for cloud integration.
- This trend towards connected safety solutions signifies a shift from traditional methods to more sophisticated, networked systems that ensure comprehensive workplace safety.
- These advancements are not just limited to technology but also encompass strategic collaborations and expansions. CO2Meter, for instance, has successfully expanded its capabilities to monitor over 40 different gases, a move that underscores the growing demand for versatile and comprehensive gas detection solutions.
- Overall, the gas detection equipment market is poised for significant growth, with innovations aimed at enhancing safety and efficiency across various industrial applications.
(Source: Ind Sci, gasworld)
Regulations and Statistics for Gas Detection Equipment
- Regulations for gas detection equipment vary significantly across countries, reflecting the diverse industrial standards and safety requirements globally.
- In the United States, recent updates include the EPA’s implementation of new performance standards aimed at reducing methane and volatile organic compound emissions from the oil and gas sector, utilizing advanced technologies like Gas Mapping LiDAR for regulatory compliance.
- The European Union, on the other hand, has tightened regulations around methane emissions, requiring detailed data from producers to meet the EU’s MMRV standards, emphasizing the need for harmonization with major exporters to prevent supply disruptions.
- In Ireland, the focus extends beyond natural gas, addressing various gases like propane and butane, with a significant emphasis on risk assessments and safety protocols tailored to specific uses. This proactive approach is necessary due to the gaps in compliance guidelines for non-natural gases.
- Similarly, in the UK and Europe, regulations such as the Safe Work in Confined Spaces, HSE Confined Spaces Regulations, and EH40 workplace exposure limits are crucial for ensuring safety in workplaces involving gas risks.
- Moreover, key examples of developments include the use of infrared and laser-based leak detection technologies, which are being integrated into advanced leak detection programs (ALDPs) to improve safety and efficiency in pipeline monitoring in the U.S., allowing operators to use technology that meets minimum sensitivity requirements and to evaluate new technologies as they become available.
(Source: Bridger Photonics, IOGP Europe, OBW Technologies, InterAgency Board, Highwood Emissions Management)
Recent Developments
Acquisitions and Mergers:
- Kohl’s Acquisition by Franchise Group (2023): In 2023, Franchise Group, a retail management firm, acquired Kohl’s for approximately $8 billion. This move is expected to enhance Kohl’s presence in the department store sector while also integrating new technologies to improve the shopping experience.
- Macy’s Acquires Bluestone Lane (2022): Macy’s, a leading U.S. department store chain, acquired Bluestone Lane, an Australian-inspired coffee shop chain, for $10 million in 2022. This acquisition aims to enhance Macy’s in-store experience by integrating cafés in their department stores, offering shoppers a more enjoyable and immersive shopping environment.
Product Launches:
- Target’s New Sustainability Initiative (2023): In 2023, Target launched a new collection of sustainable and eco-friendly products across various departments, including clothing, home goods, and beauty. The products are made with recycled materials and sustainable practices. The company expects to grow its sustainability-focused product range by 25% over the next 5 years.
- Walmart Launches Private Label Brand ‘Purely’ (2023): Walmart introduced a new private-label brand, “Purely,” in 2023, focusing on health-conscious food and beauty products. The launch, expected to generate $1 billion in revenue within 3 years, is aimed at attracting more health-conscious consumers who are seeking affordable organic options.
Funding and Investments:
- JCPenney’s $1 Billion Investment in E-commerce (2023): JCPenney announced in 2023 that it would invest $1 billion in expanding its e-commerce platform to enhance the online shopping experience. The company aims to increase its online sales by 50% by 2025 and compete more effectively with Amazon and other online retailers.
- Nordstrom’s $500 Million Investment in Technology (2022): Nordstrom, a prominent luxury department store, secured $500 million in funding in 2022 to improve its technology and digital platforms. This funding aims to enhance Nordstrom’s e-commerce capabilities, with plans to double its online sales by 2025.
Regulatory Developments:
- California’s New Retail Worker Protection Law (2023): In 2023, California passed a new law requiring large department stores to provide paid sick leave for workers during COVID-19 outbreaks. This law applies to companies with over 500 employees, including large chains like Macy’s and Kohl’s. This legislation is expected to raise operating costs but could also improve employee retention and satisfaction.
Conclusion
Gas Detection Equipment Statistics – The Gas Detection Equipment market is essential for ensuring safety and compliance across industries like oil and gas, healthcare, and construction.
Advancements in sensor technologies, including electrochemical, infrared, and ultrasonic sensors and the integration of IoT and AI enhance real-time monitoring and data analysis.
Growth is driven by increasing safety regulations and environmental concerns, with significant investments in regions such as North America, Europe, and Asia.
Despite challenges like high costs and frequent calibration needs, the market is set to grow as industries adopt modern technologies to improve safety and sustainability.
FAQs
Gas detection equipment is a device used to monitor and detect hazardous gases in the environment to ensure safety and compliance. It is widely used in industries like oil and gas, healthcare, manufacturing, and construction.
Common sensors include electrochemical, infrared (IR), catalytic, ultrasonic, and photoionization detectors (PID), each suited for detecting specific gases or vapors.
Gas detectors can detect a wide range of gases, including methane (CH4), carbon monoxide (CO), ammonia (NH3), hydrogen sulfide (H2S), and volatile organic compounds (VOCs).
Gas detectors use sensors to measure gas concentrations in the air. If the gas level exceeds a set threshold, the equipment triggers alarms to warn users of potential hazards.
It is used in industrial facilities, HVAC systems, chemical plants, confined spaces, laboratories, and other environments where gas leaks or emissions may occur.
Discuss your needs with our analyst
Please share your requirements with more details so our analyst can check if they can solve your problem(s)
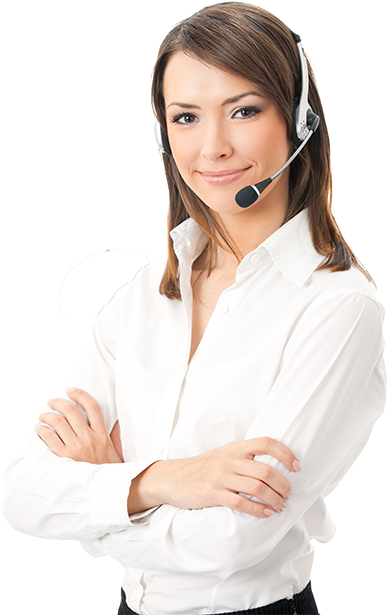