Table of Contents
Introduction
According to the Market.us, The Global Operational Predictive Maintenance Market is projected to grow significantly, with its size expected to reach approximately USD 43.3 billion by 2033, up from USD 4.5 billion in 2023. This represents a robust compound annual growth rate (CAGR) of 25.4% during the forecast period from 2024 to 2033.
Global Operational Predictive Maintenance (OPM) represents a transformative approach in maintenance management, leveraging advanced analytics and machine learning technologies to predict equipment failures before they occur. This proactive maintenance strategy is integrated into industries worldwide to enhance operational efficiency, reduce downtime, and decrease maintenance costs.
By utilizing real-time data gathered from various sensors and IoT devices, OPM systems can detect anomalies and forecast potential breakdowns, allowing businesses to undertake timely repairs and avoid costly interruptions. This shift from traditional reactive maintenance practices to a predictive approach is not just revolutionizing maintenance routines but also driving substantial economic benefits across sectors like manufacturing, energy, transportation, and more. As technology evolves, the adoption of OPM is expected to grow, underscoring its crucial role in the future of industrial operations.
The demand for global operational predictive maintenance is driven by the increasing need for efficiency and cost reduction in manufacturing and other industries. As companies strive to optimize operations and reduce unexpected downtime, the reliance on predictive maintenance grows. This demand is further bolstered by the widespread adoption of IoT devices, which provide the necessary data for effective predictive maintenance.

Several factors contribute to the growth of the operational predictive maintenance market. Technological advancements in AI and machine learning have significantly improved the accuracy of predictive analytics, making OPM solutions more reliable and effective. Additionally, the growth of industrial automation and smart factories has created a vast network of connected devices, generating large volumes of data that can be utilized for predictive maintenance. Regulatory pressures and environmental concerns also push industries to adopt more efficient and reliable maintenance strategies to ensure compliance and reduce environmental impact.
The market opportunity for operational predictive maintenance is substantial and growing, as industries across the globe recognize the cost savings and efficiency gains it offers. There is particularly strong potential in sectors such as manufacturing, aerospace, transportation, and energy, where equipment uptime is critical to operational success. The increasing sophistication of IoT technology and predictive analytics software opens up new avenues for innovation in maintenance practices, presenting significant opportunities for solution providers in this space.
Key Takeaways
- The Operational Predictive Maintenance Market was valued at USD 4.5 billion in 2023 and is anticipated to grow to USD 43.3 billion by 2033, reflecting a CAGR of 25.4%.
- In 2023, the Software segment led the market, accounting for 53.4%, due to its crucial role in data analysis and predictive algorithm development.
- Cloud deployment mode was the most popular in 2023, comprising 56.8% of the market, driven by the demand for scalable and accessible maintenance solutions.
- Manufacturing was the leading end-user segment in 2023, capturing 27.5% of the market, largely due to the vital importance of uptime and efficiency in production processes.
- North America dominated the market in 2023 with a 37.9% share, attributed to the region’s robust industrial base and emphasis on operational efficiency.
Operational Predictive Maintenance Statistics
- The Global Predictive Maintenance Market is projected to attain a valuation of approximately USD 107.3 Billion by 2033, up from USD 8.7 Billion in 2023, marking a robust compound annual growth rate (CAGR) of 28.5% over the forecast period from 2024 to 2033.
- Similarly, the Global Automotive Predictive Maintenance Market is poised for significant growth, expected to reach around USD 100 Billion by 2032 from USD 22 Billion in 2023, with a CAGR of 18.6% during the period from 2023 to 2032.
- The Global AI in Predictive Maintenance Market size is also anticipated to experience substantial growth, projected to be approximately USD 2,306.2 Million by 2033, up from USD 722.9 Million in 2023. This market is expected to grow at a CAGR of 12.3% during the forecast period from 2024 to 2033.
- Inefficiencies in maintenance strategies can lead to a reduction in a facility’s overall productive capacity by 5% to 20%.
- Adopting predictive maintenance strategies can result in savings of 30-40% compared to reactive maintenance, or savings of 8-12% compared to preventive maintenance.
- Currently, 47% of global manufacturers implement predictive maintenance technologies to curtail operational costs, indicating significant growth potential as the remaining 53% have yet to adopt these technologies.
- In the European market, companies are currently facing several critical challenges related to asset management and maintenance. The primary concerns include 90% of firms grappling with unplanned downtime and emergency maintenance, 88% dealing with ageing IT infrastructure and technology, and 76% facing difficulties in connecting modern assets and analyzing their data.
- Additional issues highlighted include obtaining asset data (40%), integrating older legacy assets to extract useful data (29%), optimizing maintenance cycles (24%), managing assets from remote locations (24%), real-time monitoring of assets (22%), and enhancing collaboration with vendors (20%).
- Deloitte’s analysis suggests substantial potential for cost savings and efficiency improvements. Firms can achieve 5%–10% in material cost savings on operations, maintenance, repair, and operations (MRO) material spend. Inventory carrying costs could be reduced by 5%–20%, while equipment uptime and availability might increase by 10%–20%.
- Furthermore, there could be a 20%–50% reduction in maintenance planning time, accompanied by a 5%–10% decrease in overall maintenance costs. These efficiencies underscore the significant opportunities for European companies to enhance their asset management strategies and operations.
Emerging Trends
- Artificial Intelligence (AI) Enhancement: AI continues to transform predictive maintenance by enabling real-time data analysis and identifying potential equipment failures, thus optimizing maintenance schedules and reducing downtime.
- Internet of Things (IoT) Expansion: IoT technologies are increasingly used for centralized asset monitoring, providing real-time data that facilitates proactive maintenance interventions before issues escalate into costly failures.
- Advanced Inspection Technologies: Techniques such as vibration analysis and infrared thermography are becoming more sophisticated, allowing for a more comprehensive assessment of equipment health and early detection of issues.
- Predictive Analytics: The use of advanced algorithms and machine learning in predictive analytics helps in analyzing vast amounts of data to foresee equipment health and anticipate maintenance needs.
- Immersive Technologies: Technologies like Extended Reality (XR) are redefining asset inspections by integrating virtual and augmented reality tools into maintenance workflows, enhancing precision and efficiency in maintenance operations.
Top Use Cases
- Equipment Failure Prediction: AI and machine learning enable predictive maintenance systems to forecast equipment failures, allowing maintenance to be performed only when necessary, thus minimizing downtime and extending equipment life.
- Maintenance Schedule Optimization: By monitoring real-time conditions of equipment rather than relying on fixed intervals, predictive maintenance optimizes maintenance tasks and schedules, enhancing operational efficiency.
- Energy Management: Predictive maintenance is applied to identify energy-intensive equipment and optimize its performance, contributing to significant energy savings and achieving sustainability goals.
- Fleet Management Enhancement: In transportation, predictive maintenance helps in predicting vehicle maintenance needs, improving safety, and reliability of fleet operations.
- Infrastructure Monitoring in Energy Sector: In the energy sector, predictive maintenance is crucial for monitoring infrastructure to prevent failures that could result in large-scale outages, ensuring continuous and reliable energy supply.
Major Challenges
- Data Overload and Analysis: One of the primary challenges in implementing predictive maintenance is managing the sheer volume of data generated by manufacturing operations. This data needs to be analyzed to identify usable patterns that can predict equipment failures, which requires sophisticated analytical tools and skills.
- Integration with Existing Systems: Integrating new predictive maintenance technologies with existing manufacturing systems and infrastructure can be problematic. Compatibility issues may arise, making it difficult to ensure smooth data flow between systems, which is crucial for the successful deployment of predictive maintenance strategies.
- Skill Gap and Training: The adoption of new predictive maintenance technologies necessitates significant training to bridge the skill gap among workers. Ensuring that the workforce is proficient in these technologies is often a time-consuming and resource-intensive process.
- Cost Constraints: Financial barriers often hinder the adoption of predictive maintenance technologies, especially for smaller manufacturing firms. The initial investment for these technologies can be considerable, posing a significant challenge for budget-conscious businesses.
- Scalability: As businesses grow, their predictive maintenance systems must scale accordingly. This scalability must be managed while maintaining accuracy and efficiency across an increasing number of machines and data points, which can be a complex challenge.
Top Market Opportunities
- Enhancing Equipment Lifespan and Performance: Predictive maintenance allows businesses to proactively identify and address potential equipment issues before they lead to failures, significantly enhancing the lifespan and performance of machinery.
- Reducing Unplanned Downtime: By predicting failures before they occur, companies can plan maintenance more effectively, thereby reducing unplanned downtime and enhancing operational efficiency.
- Cost Savings: Predictive maintenance can lead to substantial cost savings by minimizing the need for expensive repairs and downtime. It also optimizes the use of maintenance resources by focusing on the most critical needs based on predictive data insights
- Improving Safety: Proactively addressing maintenance issues can significantly improve safety in manufacturing environments by reducing the risk of unexpected equipment failures that could endanger workers.
- Data-Driven Decision Making: Implementing predictive maintenance strategies allows companies to make more informed decisions based on comprehensive data analysis. This capability can transform operations from reactive to proactive, optimizing overall business strategies.
Recent Developments
- Rockwell Automation: In September 2023, Rockwell Automation introduced the Asset Risk Predictor, an AI-powered predictive maintenance tool under the Fiix brand. This tool helps organizations detect potential equipment failures days in advance by analyzing sensor data, operational environments, and machine recipes. It is designed to reduce downtime and maintenance costs by predicting asset failures more accurately and quickly.
- SAP SE: SAP continued to expand its cloud solutions in 2024, particularly with the adoption of RISE with SAP by several major companies. The focus on cloud-based operational platforms includes SAP’s Asset Performance Management solutions, which are integral for implementing predictive maintenance strategies. This aligns with SAP’s broader goal of supporting digital transformation in various industries.
Conclusion
In conclusion, Global Operational Predictive Maintenance (OPM) is at the forefront of industrial innovation, offering a strategic advantage by enhancing the reliability and efficiency of equipment maintenance. With its ability to anticipate failures before they occur, OPM not only safeguards critical infrastructure but also supports sustainable practices by reducing waste and optimizing resource use. The integration of IoT, AI, and machine learning technologies continues to propel the OPM market forward, making it an indispensable tool in a wide range of industries, from manufacturing to transportation.
As more organizations recognize the benefits of predictive maintenance, the adoption of OPM is expected to accelerate, further driving advancements in this field and reshaping maintenance strategies across the global industrial landscape. This evolution underscores the growing importance of predictive maintenance as a key component of modern operational strategies, ensuring businesses remain competitive in an increasingly automated and data-driven world.
Discuss your needs with our analyst
Please share your requirements with more details so our analyst can check if they can solve your problem(s)
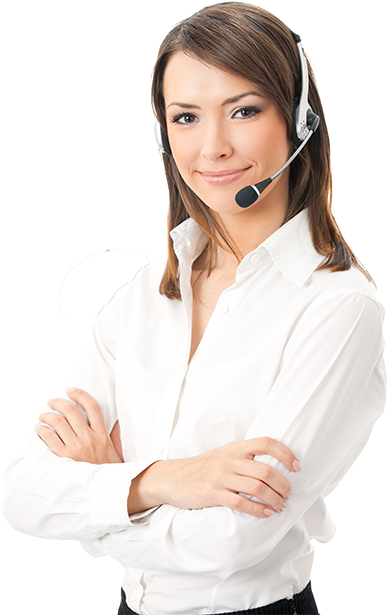